Manufacturing method of washer
A manufacturing method and technology of Wasser, applied in the direction of engine components, mechanical equipment, etc., can solve problems such as interruption of high-speed mass production, shortened service life of molds and fixtures, and large material deformation, so as to prolong service life and improve mechanical properties , the effect of slowing down the speed
- Summary
- Abstract
- Description
- Claims
- Application Information
AI Technical Summary
Problems solved by technology
Method used
Image
Examples
Embodiment Construction
[0031] The present invention will be described in detail below in conjunction with the accompanying drawings and embodiments.
[0032] refer to image 3, the first preferred embodiment of the washer manufacturing method of the present invention is to use a forging equipment 3 to forge a wire 4 into a washer finished product 5. The forging equipment 3 includes a first forging device 31 and a second forging device 32, and a third punching device 33. The first punching device 31 includes a first female die 312 with a first die cavity 311, and a first male die 314 with a first punch 313 that can be driven to move toward the first female die 312 . The second punching device 32 includes a second female die 322 with a second die cavity 321, and a second male die 324 that has a second punch 323 and can be driven to move toward the second female die 322. . The third forging device 33 includes a third female die 332 having a through hole 331 , and a third male die 334 having a third...
PUM
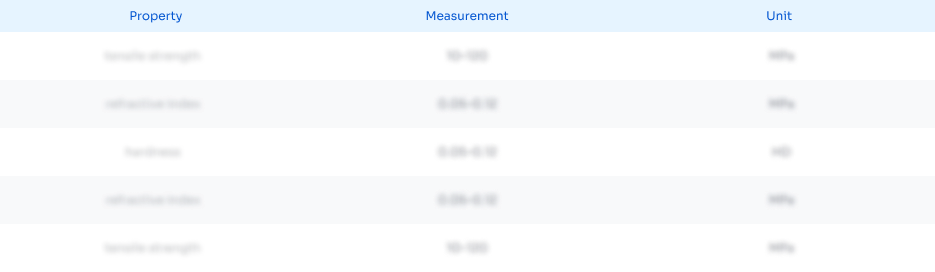
Abstract
Description
Claims
Application Information

- R&D
- Intellectual Property
- Life Sciences
- Materials
- Tech Scout
- Unparalleled Data Quality
- Higher Quality Content
- 60% Fewer Hallucinations
Browse by: Latest US Patents, China's latest patents, Technical Efficacy Thesaurus, Application Domain, Technology Topic, Popular Technical Reports.
© 2025 PatSnap. All rights reserved.Legal|Privacy policy|Modern Slavery Act Transparency Statement|Sitemap|About US| Contact US: help@patsnap.com