Pretreatment process for producing bamboo fibers with bamboos
A pretreatment and bamboo fiber technology, which is applied in the direction of fiber raw material treatment, pretreatment with alkaline compounds, finely split raw material pretreatment, etc., can solve the problems of large hydrogen peroxide consumption and long bleaching process time, and achieve saving Effects of steam and medicine, shortened reaction time, and reduced dosage
- Summary
- Abstract
- Description
- Claims
- Application Information
AI Technical Summary
Problems solved by technology
Method used
Image
Examples
Embodiment 1
[0013] The pretreatment process of bamboo to produce bamboo fiber is as follows: first cut the whole bamboo into 2m long, wash off the soil and impurities with water, and after screening, crush it into 1.5t bamboo chips with a maximum diameter of 2cm or 3cm in length.
[0014] Add 6t of soaking water to the soaking tank, then add 60Kg of NaOH and 45g of biological enzyme, the biological enzyme is a mixture of laccase and xylanase, wherein 30g of laccase and 15g of xylanase.
[0015] Heat the water in the soaking pool to 60-80°C, put the bamboo slices in, soak for 4 hours, remove them, and turn them into filaments by a wire separator for pulping.
[0016] Soaking water is reused after sedimentation and membrane treatment.
[0017] The bamboo chip that embodiment 1 handles and the bamboo chip of conventional hydrolysis treatment compare the following table in the effect of the later stage bleaching treatment stage:
[0018]
Embodiment 2
[0020] The pretreatment process of bamboo to produce bamboo fiber is as follows:
[0021] The pretreatment process of bamboo to produce bamboo fiber is as follows: first cut the whole bamboo into 2m long, wash off the soil and impurities with water, and after screening, crush it into 1.5t bamboo chips with a maximum diameter of 2cm or 3cm in length.
[0022] Add 9t of soaking water to the soaking tank, then add 360Kg of NaOH and 105g of biological enzyme, the biological enzyme is a mixture of laccase and xylanase, wherein 75g of laccase and 30g of xylanase.
[0023] Heat the water in the soaking pool to 60-80°C, put the bamboo slices in, soak for 8 hours, remove them, and turn them into filaments by a wire separator for pulping.
[0024] Soaking water is reused after sedimentation and membrane treatment.
[0025] The bamboo chip that embodiment 2 handles and the bamboo chip of conventional hydrolysis treatment compare the following table in the effect of the later stage bleac...
PUM
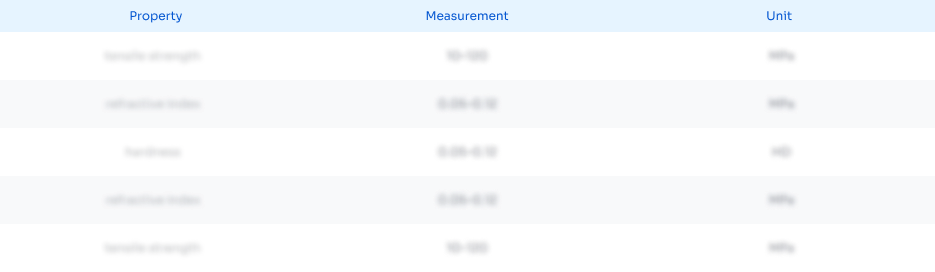
Abstract
Description
Claims
Application Information

- R&D Engineer
- R&D Manager
- IP Professional
- Industry Leading Data Capabilities
- Powerful AI technology
- Patent DNA Extraction
Browse by: Latest US Patents, China's latest patents, Technical Efficacy Thesaurus, Application Domain, Technology Topic, Popular Technical Reports.
© 2024 PatSnap. All rights reserved.Legal|Privacy policy|Modern Slavery Act Transparency Statement|Sitemap|About US| Contact US: help@patsnap.com