Gravity center self-balance device for high-order picking truck
A technology for balancing devices and picking vehicles, which is applied in the direction of lifting devices, etc., which can solve the problems affecting vehicle mobility, large vehicle body structure, and increased vehicle weight, and achieve the effects of weight reduction, vehicle volume reduction, and energy saving
- Summary
- Abstract
- Description
- Claims
- Application Information
AI Technical Summary
Problems solved by technology
Method used
Image
Examples
Embodiment Construction
[0014] The present invention will be described in further detail below in conjunction with the accompanying drawings and specific embodiments.
[0015] see figure 1 , the movable counterweight mechanism is made up of counterweight mechanism base 401, longitudinal movement mechanism, transverse movement mechanism and counterweight device, wherein the linear guide rails 402, 416 of the longitudinal movement mechanism and the transverse movement mechanism become 90 degrees and are set up and down in two layers.
[0016] see figure 2 , the high-position sorting vehicle is mainly composed of a chassis unit 1, a gantry system 2 and a liftable operation platform 3. During the working process, it includes goods 8 and a driver 9. The wheels include driving wheels 5, left rear wheels 6 and right rear wheels 7. A movable counterweight mechanism 4 is arranged below the chassis unit 1 , and a controller 10 is arranged above the chassis unit 1 .
[0017] The specific embodiment of the pr...
PUM
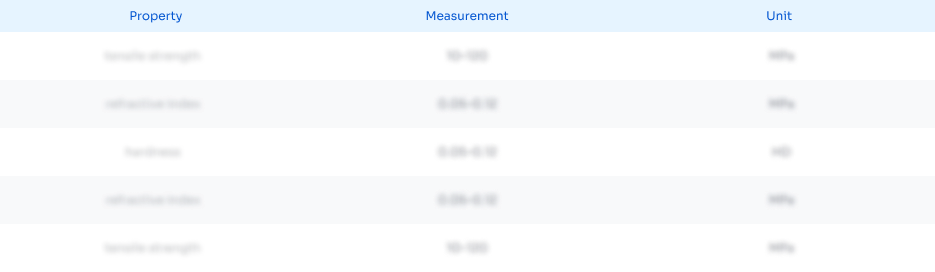
Abstract
Description
Claims
Application Information

- R&D Engineer
- R&D Manager
- IP Professional
- Industry Leading Data Capabilities
- Powerful AI technology
- Patent DNA Extraction
Browse by: Latest US Patents, China's latest patents, Technical Efficacy Thesaurus, Application Domain, Technology Topic, Popular Technical Reports.
© 2024 PatSnap. All rights reserved.Legal|Privacy policy|Modern Slavery Act Transparency Statement|Sitemap|About US| Contact US: help@patsnap.com