Cavity machining track planning method based on numerical control operation system
A trajectory planning and operating system technology, applied in general control systems, control/adjustment systems, program control, etc., can solve the problems of inconsistency in surface quality and roughness of groove and cavity machining, and ensure the machining surface quality, high efficiency and flexibility. processing effect
- Summary
- Abstract
- Description
- Claims
- Application Information
AI Technical Summary
Problems solved by technology
Method used
Image
Examples
specific Embodiment approach 1
[0031] Specific implementation one: as Figures 1 to 10 As shown, the groove machining trajectory planning method based on the numerical control operating system described in this embodiment is implemented according to the following steps:
[0032] Step A. Based on the longitudinal section depth direction boundary trajectory of the groove on the drawing, the longitudinal section diagram combined line segment composed of straight lines and circular arcs is used to calculate the number of machining paths n (parameter R in the program) of the tool in the depth direction. 7 ) as the set condition variable to plan a set of uniformly arranged point sets projected on the combined line segment of the longitudinal section diagram, the distance between each adjacent two points is the step of the projection of the distance between the two adjacent trajectories on the combined line segment of the longitudinal section diagram. The long value M, and then control the uniform arrangement of t...
specific Embodiment approach 2
[0058] Specific implementation two: see image 3 , the groove machining trajectory planning method based on the numerical control operating system described in this embodiment further includes step B: calculating the groove side fixed cutting edge of the tool on the basis of selecting a suitable tool according to the trajectory planned in step A (1 ), the compensation value of the dynamic cutting edge (2) of the groove fillet surface and the tool setting point (O) of the tool to describe the trajectory of the tool setting point; the suitable tool means that the fillet of the tool is smaller than the groove to be machined the corner radius R. Other steps are the same as in the first embodiment.
[0059] Tool selection: Because the side wall of the groove is straight, and the bottom edge is rounded, it is more appropriate to use a rounded end mill, which can not only improve the processing efficiency of the side wall, but also meet the surface quality of the rounded face. , so...
specific Embodiment approach 3
[0060] Specific implementation three: as Figures 1 to 5 and Image 6 As shown, this embodiment is a specific process of programming using the method of the present invention:
[0061] Step 1. Planning method for evenly arranging the trajectory of the edge rounded groove:
[0062] Based on the known dimensions of the groove on the drawing (see Figure 4 ) Considering that the longitudinal section boundary trajectory of the groove is a combination curve of a straight line and a circular arc process, through a series of calculation methods, according to the number of machining trajectories n (parameter R in the program) in the depth direction of the tool 7 ) setting to plan a set of evenly arranged point sets projected on the combined line of the longitudinal section, and then control the projection of the cutting path of the tool to be evenly arranged on the inner surface of the groove (see Image 6 ).
[0063] Step 2: Calculate the compensation value of the cutting point a...
PUM
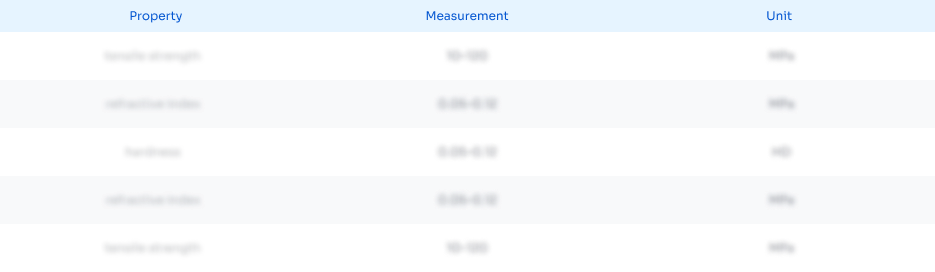
Abstract
Description
Claims
Application Information

- R&D Engineer
- R&D Manager
- IP Professional
- Industry Leading Data Capabilities
- Powerful AI technology
- Patent DNA Extraction
Browse by: Latest US Patents, China's latest patents, Technical Efficacy Thesaurus, Application Domain, Technology Topic, Popular Technical Reports.
© 2024 PatSnap. All rights reserved.Legal|Privacy policy|Modern Slavery Act Transparency Statement|Sitemap|About US| Contact US: help@patsnap.com