Grid-connection control method of grid-side converter of small permanent magnet direct-driven wind power system
A grid-side converter, permanent magnet direct drive technology, applied in the direction of single grid parallel feeding arrangement, etc., can solve the problems of long system response time, large PI control overshoot, linear sliding mode control chattering phenomenon, etc. The effect of short system response time, small overshoot and superior dynamic performance
- Summary
- Abstract
- Description
- Claims
- Application Information
AI Technical Summary
Problems solved by technology
Method used
Image
Examples
specific Embodiment approach 1
[0015] Specific implementation mode 1. Combination Figure 7 Describe this specific implementation mode, the grid-connected control method of the grid-side converter of the small permanent magnet direct drive wind power system, and the specific method is as follows:
[0016] Step 1, collecting three-phase voltage signals and three-phase current signals of the power grid, and converting them into two-phase rotating voltage signals and two-phase rotating current signals;
[0017] Step 2. Obtain the given current of the d-axis
[0018] Step 3. According to the d-axis given current obtained in step 2 Get the d-axis high-order non-singular terminal sliding mode surface s 1 , given the current according to the q-axis Get the q-axis high-order non-singular terminal sliding mode surface s 2 ;
[0019] Step 4. According to the q-axis high-order non-singular terminal sliding mode surface s obtained in step 3 2 Get the q-axis control law u q , according to the d-axis high-orde...
specific Embodiment approach 2
[0021] Specific embodiment two, combine Figure 7 Describe this specific implementation mode. The difference between this embodiment mode and specific implementation mode 1 is that the specific method of step 1 is:
[0022] Step a, collecting three-phase static voltage signal e a 、e b 、e c , input into the Clark module, and output the two-phase static voltage signal e α 、e β , the three-phase static voltage signal e a 、e b 、e c Input the PLL module, output the position signal θ, and collect the three-phase static current signal i a i b i c , input into the Clark module, and output the two-phase quiescent current signal i α i β ;
[0023] Step b, the two-phase static voltage signal e α 、e β and the position signal θ are input to the Park module, and the two-phase rotating voltage signal e is output d 、e q , the two-phase quiescent current signal i α i β and the position signal θ are input to the Park module, and the two-phase rotating current signal i is outpu...
specific Embodiment approach 3
[0024] Specific embodiment three, combine Figure 7 Describe this specific embodiment. The difference between this embodiment and specific embodiment 1 is that the specific method of step 2 is: the d-axis outer ring sets the DC bus voltage Feedback d-axis outer loop DC bus voltage u dc Obtain the difference, the difference is adjusted by PI to form the given current of the d-axis inner ring
PUM
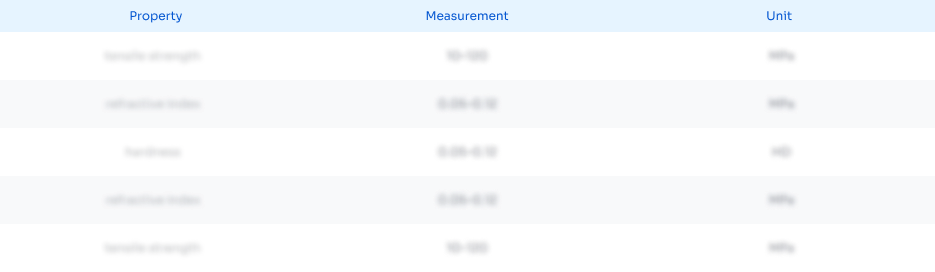
Abstract
Description
Claims
Application Information

- R&D
- Intellectual Property
- Life Sciences
- Materials
- Tech Scout
- Unparalleled Data Quality
- Higher Quality Content
- 60% Fewer Hallucinations
Browse by: Latest US Patents, China's latest patents, Technical Efficacy Thesaurus, Application Domain, Technology Topic, Popular Technical Reports.
© 2025 PatSnap. All rights reserved.Legal|Privacy policy|Modern Slavery Act Transparency Statement|Sitemap|About US| Contact US: help@patsnap.com