Production process of aliphatic polyetheramine
A production process and aliphatic technology, applied in the field of polymer materials, can solve the problems of strict reaction conditions, easy self-polymerization of acrylonitrile, and practical operation difficulties, and achieve the effects of good selectivity, convenient post-processing, and less environmental pollution
- Summary
- Abstract
- Description
- Claims
- Application Information
AI Technical Summary
Problems solved by technology
Method used
Examples
Embodiment 1
[0050] Make 1.3~1.5 times of NaOH into a 20% aqueous solution, put it into a stainless steel three-neck flask equipped with a thermometer, cool it to 50°C with running water, and add Ni-Al alloy to it in batches under vigorous stirring (each 2~4g each time), the addition is completed within 25~30min. Adjust the speed of adding the alloy so that the temperature of the liquid is kept around 50°C. After the feeding is completed, react at about 80°C for about 90 minutes while stirring. After the production of hydrogen is completed and the mixture is still, the white flocculent reaction product in the upper layer is separated, and the precipitated black Raney nickel catalyst is moved to a beaker, and washed with water until the lotion is neutral to litmus. Then wash with 95% ethanol and absolute ethanol for 2 to 3 times respectively, and finally put them in a container with a closed stopper in absolute ethanol.
Embodiment 2
[0052] Add 100g of hydroxyl-terminated polyoxypropylene ether (polyether department of Tianjin Petrochemical Co., Ltd.) with a number average molecular weight of 230.8 and a functionality of 2 into a 0.5L autoclave, and 10g of a special skeleton nickel catalyst. Replace the reactor with 0.4MPa nitrogen and hydrogen for 2 to 3 times respectively, pour about 43L of ammonia into the reactor under stirring (under standard conditions), adjust the outlet pressure of the hydrogen cylinder to 4.0MPa, and fill the reactor with hydrogen When the pressure is balanced, the temperature is raised by heating, and the reaction temperature is controlled at 200° C., the reaction time is 4 hours, and the maximum reaction pressure is 13.0 MPa. After the reaction, pass cooling water until the temperature of the reactor is 50°C, slowly exhaust, the gas is absorbed by the secondary water, and the material is discharged.
[0053] Filter the reaction solution while it is hot to separate the catalyst a...
Embodiment 3
[0055] Add 100g of hydroxyl-terminated polyoxypropylene ether (polyether department of Tianjin Petrochemical Co., Ltd.) with a number average molecular weight of 230.8 and a functionality of 2 into a 0.5L autoclave, and 15g of a special skeleton nickel catalyst. Replace the reactor with 0.4MPa nitrogen and hydrogen for 2 to 3 times respectively, pour about 43L of ammonia into the reactor under stirring (under standard conditions), adjust the outlet pressure of the hydrogen cylinder to 4.0MPa, and fill the reactor with hydrogen When the pressure is balanced, the temperature is raised by heating, and the reaction temperature is controlled at 200° C., the reaction time is 4 hours, and the maximum reaction pressure is 12.5 MPa. After the reaction, pass cooling water until the temperature of the reactor is 50°C, slowly exhaust, the gas is absorbed by the secondary water, and the material is discharged.
[0056] Filter the reaction solution while it is hot to separate the catalyst a...
PUM
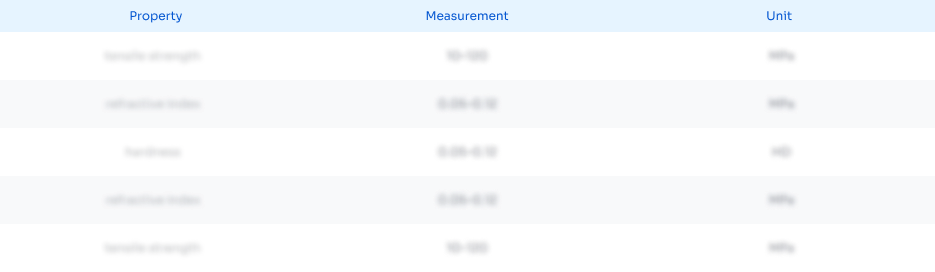
Abstract
Description
Claims
Application Information

- R&D
- Intellectual Property
- Life Sciences
- Materials
- Tech Scout
- Unparalleled Data Quality
- Higher Quality Content
- 60% Fewer Hallucinations
Browse by: Latest US Patents, China's latest patents, Technical Efficacy Thesaurus, Application Domain, Technology Topic, Popular Technical Reports.
© 2025 PatSnap. All rights reserved.Legal|Privacy policy|Modern Slavery Act Transparency Statement|Sitemap|About US| Contact US: help@patsnap.com