Two-finger flexible micro clamper
A two-finger flexible and dynamic clamping technology, applied in the mechanical field, can solve the problems of performance limitation, limited deformation, less flexible structure, etc., and achieve the effect of micro-feeding and precise positioning, eliminating nonlinearity and compact structure
- Summary
- Abstract
- Description
- Claims
- Application Information
AI Technical Summary
Problems solved by technology
Method used
Image
Examples
Embodiment Construction
[0018] Hereinafter, the present invention will be described in further detail in combination with preferred embodiments and the accompanying drawings.
[0019] The two-finger flexible micro-movement gripper (referred to as the gripper, see Figure 1-4 ), mainly including four flexible branch chains with the same structure 1, a base with a boss 2, an "H"-shaped connecting beam 3, a symmetrical "["-shaped connecting beam 41 and a "】"-shaped connecting beam 42. A piezoelectric ceramic driver 5, two "J"-shaped gripping fingers (referred to as gripping fingers) 6, a capacitive displacement sensor 7 and a spherical joint 8;
[0020] The embodiment of the base 2 of the present invention is a rectangular plate structure (see image 3 ), there is a boss in the middle of one long side edge, a threaded through hole 21 is opened horizontally in the middle of the boss, and the other three sides have vertical mounting holes 22 (2 on the long side and 2 on the short side). 1 each), the so-called...
PUM
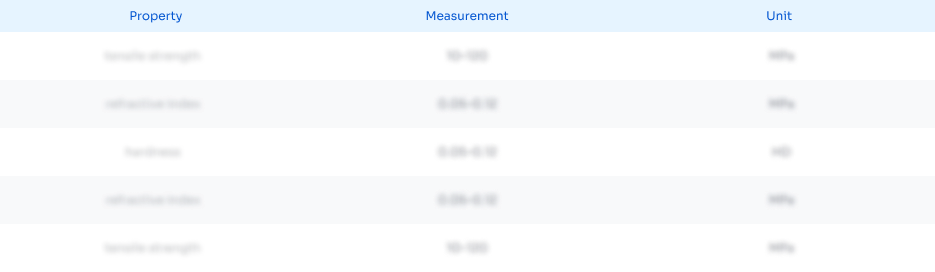
Abstract
Description
Claims
Application Information

- R&D
- Intellectual Property
- Life Sciences
- Materials
- Tech Scout
- Unparalleled Data Quality
- Higher Quality Content
- 60% Fewer Hallucinations
Browse by: Latest US Patents, China's latest patents, Technical Efficacy Thesaurus, Application Domain, Technology Topic, Popular Technical Reports.
© 2025 PatSnap. All rights reserved.Legal|Privacy policy|Modern Slavery Act Transparency Statement|Sitemap|About US| Contact US: help@patsnap.com