Turning mechanism in machining of large ship propeller shafts
A technology for stern shafts and ships, which is applied in the field of turning devices in the processing of large ship stern shafts. It can solve the problems of inability to increase the rigidity of parts, improper pressure of parts, and reduced processing accuracy, so as to reduce friction and heat generation during cutting, and reduce heat generation. The effect of increasing the turning speed
- Summary
- Abstract
- Description
- Claims
- Application Information
AI Technical Summary
Problems solved by technology
Method used
Image
Examples
Embodiment Construction
[0010] A turning device in the processing of a large ship stern shaft is a lathe with a chuck at the head of the bed, a thimble at the end of the bed, and a center support. An axial feed mechanism is installed on the bed rail. A knife rest is respectively installed on the radial feed mechanism, and a follower rest is also installed on the axial feed mechanism. The installation position of the tool holder relative to the stern shaft is as follows: figure 1 , 2 As shown, the feeding direction of the turning tool 2 on the two tool holders points to the axis of the stern shaft 1 from downward obliquely upward, and each is on the radial line of 60° between the vertical plane of the axis. At the same time, the two turning tools There is a gap in the length direction of the shaft, that is, there are front and rear for the cutting point of the shaft. The emitters of the three laser rangefinders point to the axis of the stern shaft, which are in the same direction as the feed directi...
PUM
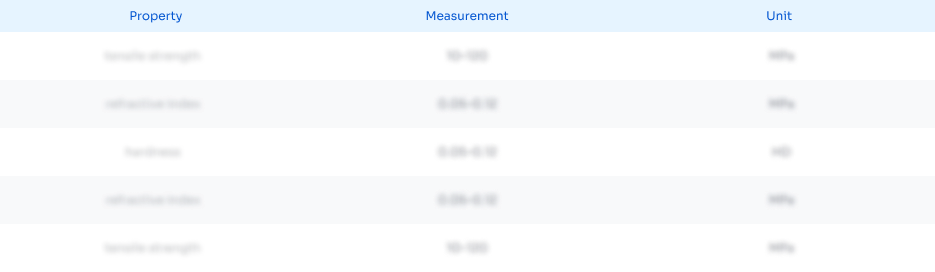
Abstract
Description
Claims
Application Information

- R&D
- Intellectual Property
- Life Sciences
- Materials
- Tech Scout
- Unparalleled Data Quality
- Higher Quality Content
- 60% Fewer Hallucinations
Browse by: Latest US Patents, China's latest patents, Technical Efficacy Thesaurus, Application Domain, Technology Topic, Popular Technical Reports.
© 2025 PatSnap. All rights reserved.Legal|Privacy policy|Modern Slavery Act Transparency Statement|Sitemap|About US| Contact US: help@patsnap.com