Preparation method of composite conductive fabric with spray polymerization
A technology of composite conduction and spray polymerization, which is applied in the field of textiles, can solve the problems that the polypyrrole layer of the composite conductive fabric is not uniform and dense, the wear resistance and solvent resistance need to be improved, and it is unfavorable for large-scale industrial production, and the probability of achieving the reaction is high. , Stable conductivity, good conductivity effect
- Summary
- Abstract
- Description
- Claims
- Application Information
AI Technical Summary
Problems solved by technology
Method used
Image
Examples
Embodiment 1
[0030]According to the above-mentioned preparation method, under room temperature, prepare an oxidation initiation system solution composed of ferric chloride and deionized water, wherein the concentration of ferric chloride is 0.2mol / L, and the bath ratio of cotton fabric is 1:40 Put it into the prepared oxidation initiating system solution, soak the fabric for 1 hour, take it out and dry it in the air, and soak it repeatedly for 30 minutes. Mix sodium dodecylbenzenesulfonate and deionized water into a beaker, stir well to form a monomer solution, wherein the concentration of pyrrole monomer is 0.1mol / L, and the concentration of sodium dodecylbenzenesulfonate is 0.60mol / L, put the prepared monomer solution into the reaction vessel A with a nebulizer, the upper port of the reaction vessel A is connected to the reaction vessel B and the nitrogen bottle through the pipeline, open the nitrogen bottle, and input into the reaction vessel A Nitrogen at a pressure of 0.5 MPa, adjust...
Embodiment 2
[0032] According to the above-mentioned preparation method, under room temperature, prepare an oxidation initiation system solution composed of ferric chloride and deionized water, wherein the concentration of ferric chloride is 0.5mol / L, and the bath ratio of silk fabric is 1:10 Put it into the prepared oxidation initiating system solution, soak the fabric for 1 hour, take it out to dry, and take it out after repeated soaking for 30 minutes. Mix body, sodium alkylnaphthalene sulfonate and deionized water into a beaker, stir well to form a monomer solution, wherein the concentration of pyrrole monomer is 0.5mol / L, and the concentration of sodium alkylnaphthalenesulfonate is 0.05mol / L , the prepared monomer solution is poured into the reaction vessel A with the atomizer, the upper port of the reaction vessel A is connected to the reaction vessel B and the nitrogen cylinder through the pipeline, the nitrogen cylinder is opened, and the input pressure in the reaction vessel A is ...
Embodiment 3
[0034] According to the above-mentioned preparation method, under room temperature conditions, prepare an oxidation initiation system solution composed of ferric chloride and deionized water, wherein the concentration of ferric chloride is 1.2mol / L, and the bath ratio of wool fabric is 1:20 Put it into the prepared oxidation initiating system solution, soak the fabric for 1 hour, take it out and dry it in the air, and soak it repeatedly for 30 minutes. Mix toluenesulfonic acid and deionized water into a beaker, stir fully to form a monomer solution, wherein the concentration of pyrrole monomer is 1.0mol / L, and the concentration of toluenesulfonic acid is 0.3mol / L. The prepared monomer solution, Pour it into the reaction vessel A with the nebulizer, the port of the reaction vessel A is connected to the reaction vessel B and the nitrogen bottle through the pipeline, open the nitrogen bottle, input the nitrogen gas with a pressure of 2.5MPa into the reaction vessel A, adjust the n...
PUM
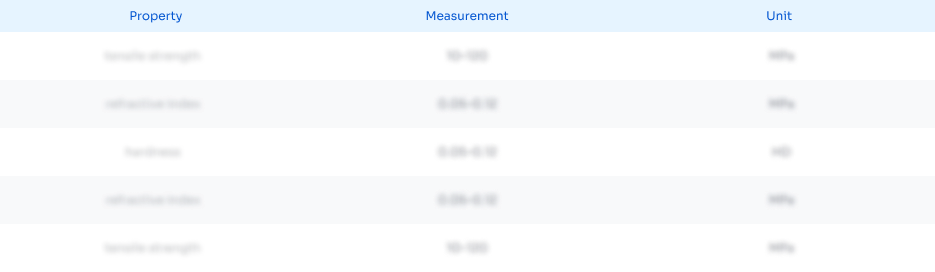
Abstract
Description
Claims
Application Information

- Generate Ideas
- Intellectual Property
- Life Sciences
- Materials
- Tech Scout
- Unparalleled Data Quality
- Higher Quality Content
- 60% Fewer Hallucinations
Browse by: Latest US Patents, China's latest patents, Technical Efficacy Thesaurus, Application Domain, Technology Topic, Popular Technical Reports.
© 2025 PatSnap. All rights reserved.Legal|Privacy policy|Modern Slavery Act Transparency Statement|Sitemap|About US| Contact US: help@patsnap.com