Preparation method of CuW70 contact material
A contact material and mixing technology, used in electrical components, electrical switches, circuits, etc., can solve the problem of uneven distribution of Cu and W phases, and achieve improved arc ablation resistance, uniform force, and uniform distribution. Effect
- Summary
- Abstract
- Description
- Claims
- Application Information
AI Technical Summary
Problems solved by technology
Method used
Image
Examples
preparation example Construction
[0019] A preparation method of CuW70 contact material, the method is carried out as follows:
[0020] Step 1: Weigh the induced copper powder and the tungsten powder respectively according to the mass percentage of the induced copper powder in the tungsten powder as 5% to 8%, and put them into a mixing tank. The addition of induced copper powder, on the one hand, can improve the formability of the brittle powder and make the pore distribution in the tungsten compact (green body) more uniform; on the other hand, in the subsequent infiltration process, the induction in the porous skeleton of the tungsten compact Copper powder melts first, forming connected pores inside the skeleton, and "lures" the molten metal to be infiltrated into the skeleton. The driving force of this fusion of internal and external molten metal will facilitate the infiltration process, thereby improving the yield of the material. density.
[0021] Step 2: Add volatile organic solvent industrial ethanol in...
Embodiment 1
[0027] Weigh the induced copper powder and tungsten powder respectively according to the mass percentage of the induced copper powder in the tungsten powder as 8%, and put them into the mixing tank. Then add industrial ethanol in the mixing tank as a mixing process control agent until the powder has a wet feeling. Add non-equal diameter grinding balls for mixing according to twice the total mass of tungsten powder and copper powder. The diameters of the grinding balls are 8mm and 4mm respectively, and the mass ratio of the two kinds of grinding balls is 1:1.5. The mixing time was controlled at 7 hours to obtain mixed powder. Pour the mixed powder into the rubber sheath, and place a cotton felt pad or filter paper for filtering between the powder material surface and the rubber end plug of the rubber sheath. After the jacket mold is filled with powder, an end seal is applied to the filling port. Then use thin iron wire to bind the end plug and the seal of the rubber sheath. A...
Embodiment 2
[0029]Weigh the induced copper powder and tungsten powder respectively according to the mass percentage of the induced copper powder in the tungsten powder as 5.5%, and put them into the mixing tank. Then add industrial ethanol in the mixing tank as a mixing process control agent until the powder has a wet feeling. According to 2.1 times of the total mass of tungsten powder and copper powder, non-equal diameter grinding balls are added for mixing. The diameters of the grinding balls are 8mm and 4mm respectively, and the mass ratio of the two kinds of grinding balls is 1:1.6. The mixing time was controlled at 6.5 hours to obtain mixed powder. Pour the mixed powder into the rubber sheath, and place a cotton felt pad or filter paper for filtering between the powder material surface and the rubber end plug of the rubber sheath. After the jacket mold is filled with powder, an end seal is applied to the filling port. Then use thin iron wire to bind the end plug and the seal of the...
PUM
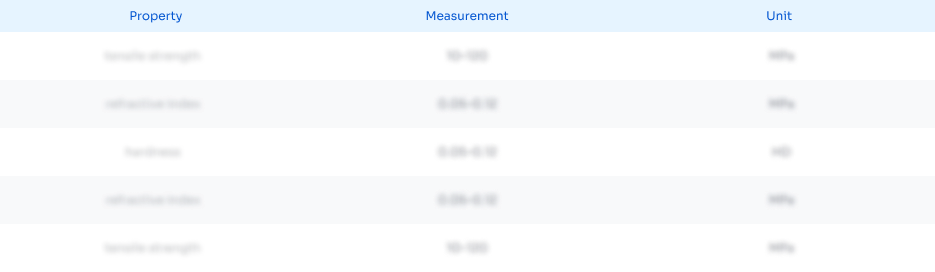
Abstract
Description
Claims
Application Information

- R&D Engineer
- R&D Manager
- IP Professional
- Industry Leading Data Capabilities
- Powerful AI technology
- Patent DNA Extraction
Browse by: Latest US Patents, China's latest patents, Technical Efficacy Thesaurus, Application Domain, Technology Topic, Popular Technical Reports.
© 2024 PatSnap. All rights reserved.Legal|Privacy policy|Modern Slavery Act Transparency Statement|Sitemap|About US| Contact US: help@patsnap.com