Method for recycling by-product 2-ethylacraldehyde from reaction process of preparing trimethylolpropane by condensing and hydrogenating method
A technology of trimethylolpropane and ethylacrolein, which is applied in the field of recovery and utilization of the by-product 2-ethylacrolein in the reaction process of preparing trimethylolpropane by condensation hydrogenation, can solve the problem of low selectivity, Affecting TMP yield and other issues, achieving high economic utilization and reducing reaction costs
- Summary
- Abstract
- Description
- Claims
- Application Information
AI Technical Summary
Problems solved by technology
Method used
Examples
Embodiment 1
[0017] According to the molar ratio of triethylamine to formaldehyde of 0.020, add 37wt% formaldehyde aqueous solution and triethylamine into the three-necked flask successively, stir and mix evenly, heat the water bath to 30°C, and then mix to the above-mentioned Add n-butyraldehyde (the molar ratio of formaldehyde to n-butyraldehyde is 2.2) dropwise into the solution, and the dropwise addition is completed within 1 hour. After the dropwise addition, continue to react at 30° C. for 2 hours, and stand to separate layers. The lower water phase is DMB, and the upper oil phase is mainly EA and butyraldehyde.
[0018] Subsequently, the upper oil phase was separated, and it was measured that the content of EA in the upper oil phase was 70%, and the content of butyraldehyde was 25%. After adding formaldehyde with 2 times the molar amount of EA therein, the pH value was adjusted to 10.0 with triethylamine, and the temperature was raised to 50° C. to continue the reaction for 5 hours....
Embodiment 2
[0020] According to the molar ratio of triethylamine to formaldehyde of 0.020, add 37wt% formaldehyde aqueous solution and triethylamine into the three-necked flask successively, stir and mix evenly, heat the water bath to 40°C, and then mix to the above-mentioned Add n-butyraldehyde (the molar ratio of formaldehyde to n-butyraldehyde is 2.2) dropwise into the solution, and the dropwise addition is completed within 1 hour. After the dropwise addition, continue to react at 30° C. for 2 hours, and stand to separate layers.
[0021] Subsequently, the upper oil phase was separated, and the content of EA and butyraldehyde was measured to be 82% and 11% respectively. After adding formaldehyde with 3 times the molar amount of EA therein, the pH value was adjusted to 10.5 with triethylamine, and the temperature was raised to 50° C. to continue the reaction for 5 hours. The selectivity is 90%.
Embodiment 3
[0023] According to the molar ratio of triethylamine to formaldehyde of 0.020, add 37wt% formaldehyde aqueous solution and triethylamine into the three-necked flask successively, stir and mix evenly, heat the water bath to 50°C, and then, under the condition of stirring, mix to the above-mentioned Add n-butyraldehyde (the molar ratio of formaldehyde to n-butyraldehyde is 3.0) dropwise to the solution, and the dropwise addition is completed within 1 hour. After the dropwise addition, continue to react at 50° C. for 2 hours, and stand to separate layers.
[0024] Subsequently, the upper oil phase was separated, and the content of EA and butyraldehyde was determined to be 90% and 6%, respectively. After adding formaldehyde with 4 times the molar amount of EA therein, adjust the pH value to 11 with triethylamine, and react at 50° C. for 5 h at the same time. After the reaction, the conversion rate of EA is measured to be 95%, and the selectivity of TMP generated is 93%.
PUM
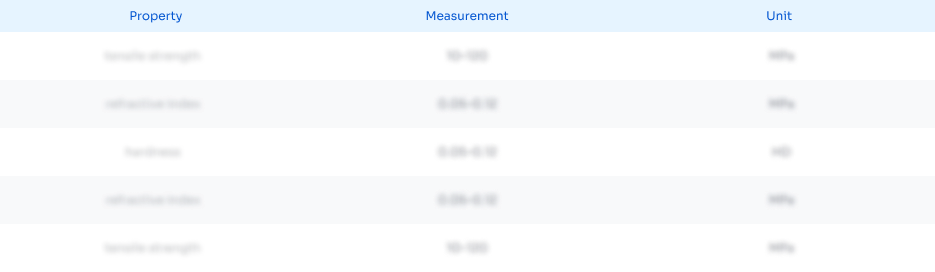
Abstract
Description
Claims
Application Information

- R&D
- Intellectual Property
- Life Sciences
- Materials
- Tech Scout
- Unparalleled Data Quality
- Higher Quality Content
- 60% Fewer Hallucinations
Browse by: Latest US Patents, China's latest patents, Technical Efficacy Thesaurus, Application Domain, Technology Topic, Popular Technical Reports.
© 2025 PatSnap. All rights reserved.Legal|Privacy policy|Modern Slavery Act Transparency Statement|Sitemap|About US| Contact US: help@patsnap.com