Horizontally-parted casting ball and casting segment mould
A technology of horizontal parting and casting, which is applied in the directions of casting mold, core, casting mold composition, etc., can solve the problems of further reduction of production cost, low utilization rate of molten iron, and low yield of product process, and achieves a reduction in production costs. High temperature blackheads, reduce the flow obstruction of molten iron, and ensure the effect of cooling and solidification
- Summary
- Abstract
- Description
- Claims
- Application Information
AI Technical Summary
Problems solved by technology
Method used
Image
Examples
Embodiment Construction
[0028] The specific implementation of the present invention is described in further detail by describing the embodiments below with reference to the accompanying drawings, so as to help those skilled in the art have a more complete, accurate and deep understanding of the inventive concept and technical solutions of the present invention.
[0029] Such as Figure 1 to Figure 4 The structure of the present invention expressed is that the present invention is a horizontal split mold for casting balls and casting sections. The present invention is mainly applicable to the casting production of casting balls and casting sections with specifications ≥Ф20. The casting ball and casting section molds include a mold body 1 with a parting surface 9 arranged in parallel, and a plurality of model strings 3 are arranged on the parting surface 9, and each model string 3 includes one or more casting balls 1. Casting section model 2, the casting ball and casting section mold are also provided ...
PUM
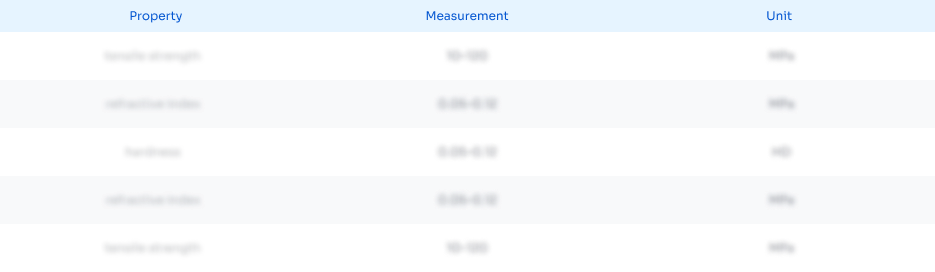
Abstract
Description
Claims
Application Information

- R&D
- Intellectual Property
- Life Sciences
- Materials
- Tech Scout
- Unparalleled Data Quality
- Higher Quality Content
- 60% Fewer Hallucinations
Browse by: Latest US Patents, China's latest patents, Technical Efficacy Thesaurus, Application Domain, Technology Topic, Popular Technical Reports.
© 2025 PatSnap. All rights reserved.Legal|Privacy policy|Modern Slavery Act Transparency Statement|Sitemap|About US| Contact US: help@patsnap.com