A core mold for spinning parts with transverse internal ribs and a method of moving back and demoulding
A mandrel and horizontal technology, which is applied in metal processing equipment, forming tools, manufacturing tools, etc., can solve the problems of increasing labor intensity of workers, large shape and size of plywood, influence of workpiece forming quality and forming accuracy, and improve forming quality and forming accuracy, easy machining and assembly, and low labor intensity for workers
- Summary
- Abstract
- Description
- Claims
- Application Information
AI Technical Summary
Problems solved by technology
Method used
Image
Examples
Embodiment 1
[0044] This implementation case is the horizontal and vertical combined split mandrel in the spin forming of a large complex thin-walled component with transverse inner ribs at the mouth of a certain spacecraft and the method of demoulding the spinning part with transverse inner ribs by moving the mold backward. The rib portion height of the workpiece rib portion 1 is between 2.5 and 2.8 mm, the axial length of the workpiece rib portion 1 is 15 mm, the axial length of the non-rib portion 2 of the workpiece is 343 mm, and the maximum diameter of the inner surface of the workpiece is 268.5 mm. The axial machining allowance of the workpiece is 30mm.
[0045] The spinning mandrel of this example includes a mandrel body 3 , a splint 4 and a collar 5 , wherein a mandrel groove 6 is located on the collar 5 , and the diameter of the mandrel groove 6 is 263.5 mm. The mandrel main body 3, the splint 4 and the collar 5 are all revolving bodies, and the splint 4 and the collar 5 are hollo...
Embodiment 2
[0054] This implementation case is the horizontal and vertical combined split mandrel in the spin forming of a large complex thin-walled component with transverse inner ribs at the mouth of a certain spacecraft and the method of demoulding the spinning part with transverse inner ribs by moving the mold backward. The rib portion height of the workpiece rib portion 1 is between 2.5 and 2.8 mm, the axial length of the workpiece rib portion 1 is 15 mm, the axial length of the non-rib portion 2 of the workpiece is 343 mm, and the maximum diameter of the inner surface of the workpiece is 268.5 mm. The axial machining allowance of the workpiece is 27.5mm.
[0055] The spinning mandrel of this example includes a mandrel body 3 , a splint 4 and a collar 5 , wherein a mandrel groove 6 is located on the collar 5 , and the diameter of the mandrel groove 6 is 263.5 mm. The mandrel main body 3, the splint 4 and the collar 5 are all revolving bodies, and the splint 4 and the collar 5 are hol...
Embodiment 3
[0064] This implementation case is the horizontal and vertical combined split mandrel in the spin forming of a large complex thin-walled component with transverse inner ribs at the mouth of a certain spacecraft and the method of demoulding the spinning part with transverse inner ribs by moving the mold backward. The rib portion height of the workpiece rib portion 1 is between 2.5 and 2.8 mm, the axial length of the workpiece rib portion 1 is 15 mm, the axial length of the non-rib portion 2 of the workpiece is 343 mm, and the maximum diameter of the inner surface of the workpiece is 268.5 mm. The axial machining allowance of the workpiece is 25mm.
[0065] The spinning mandrel of this example includes a mandrel body 3 , a splint 4 and a collar 5 , wherein a mandrel groove 6 is located on the collar 5 , and the diameter of the mandrel groove 6 is 263.5 mm. The mandrel main body 3, the splint 4 and the collar 5 are all revolving bodies, and the splint 4 and the collar 5 are hollo...
PUM
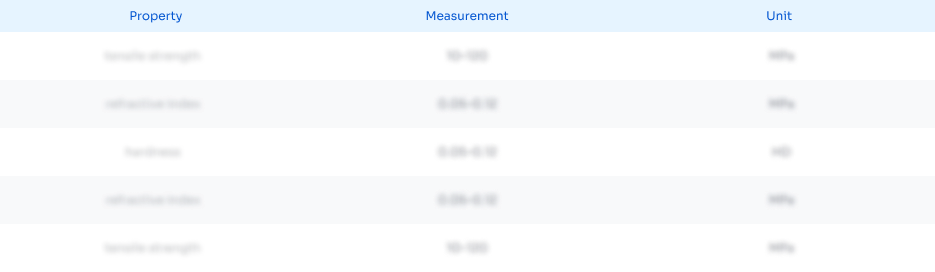
Abstract
Description
Claims
Application Information

- R&D
- Intellectual Property
- Life Sciences
- Materials
- Tech Scout
- Unparalleled Data Quality
- Higher Quality Content
- 60% Fewer Hallucinations
Browse by: Latest US Patents, China's latest patents, Technical Efficacy Thesaurus, Application Domain, Technology Topic, Popular Technical Reports.
© 2025 PatSnap. All rights reserved.Legal|Privacy policy|Modern Slavery Act Transparency Statement|Sitemap|About US| Contact US: help@patsnap.com