The beneficiation method for producing phosphate concentrate powder from low-grade phosphate rock
A beneficiation method and phosphate rock technology, applied in the field of phosphate rock beneficiation, can solve the problems of beneficiation and utilization of phosphate rock resources, excessive consumption of phosphate rock resources, etc., and achieve the effect of reducing overall costs and making full use of resources
- Summary
- Abstract
- Description
- Claims
- Application Information
AI Technical Summary
Problems solved by technology
Method used
Examples
Embodiment 1
[0012] Embodiment 1: to produce 500kg of phosphate concentrate powder, 900kg of phosphate ore with a phosphorus oxide content of 20-24% is required:
[0013] Step 1: First send the phosphate rock to the jaw crusher and crush it to less than 20mm;
[0014] Step 2: Send the crushed phosphate rock to the rotary kiln for a return calcination, and the calcination temperature is controlled at 1200-1300°C;
[0015] Step 3: After the calcined phosphate rock is quenched in the kiln tail water tank, it is sent into a ball mill to be ground into a 200-mesh slurry;
[0016] Step 4: Send the slurry to the roughing tank, add 5 kg of 1% mixed acid inhibitor and 1.44 kg of 0.16% auxiliary collector during the stirring process of the mixer to obtain 500 kg of phosphate concentrate powder deposited below.
Embodiment 2
[0017] Example 2: Calculated by producing 1000kg of phosphate concentrate powder, 2000kg of phosphate ore with a phosphorus oxide content of 20-24% is required:
[0018] Step 1: First send the phosphate rock to the jaw crusher and crush it to less than 20mm;
[0019] Step 2: Send the crushed phosphate rock to the rotary kiln for a return calcination, and the calcination temperature is controlled at 1200-1300°C;
[0020] Step 3: After the calcined phosphate rock is quenched in the kiln tail water tank, it is sent into a ball mill to be ground into a 200-mesh slurry;
[0021] Step 4: Send the slurry to the roughing tank, add 10.5kg of 1.05% mixed acid inhibitor and 1.8kg of 0.18% auxiliary collector during the stirring process of the mixer to obtain 1000kg of phosphate concentrate powder deposited below.
Embodiment 3
[0022] Embodiment 3: to produce 1500kg of phosphate concentrate powder, 2900kg of phosphate ore with a phosphorus oxide content of 20-24% is required:
[0023] Step 1: First send the phosphate rock to the jaw crusher and crush it to less than 20mm;
[0024] Step 2: Send the crushed phosphate rock to the rotary kiln for a return calcination, and the calcination temperature is controlled at 1200-1300°C;
[0025] Step 3: After the calcined phosphate rock is quenched in the kiln tail water tank, it is sent into a ball mill to be ground into a 200-mesh slurry;
[0026] Step 4: Send the slurry to the roughing tank, add 16.5kg of 1.1% mixed acid inhibitor and 3.15kg of 0.21% auxiliary collector during the stirring process of the mixer to obtain 1500kg of phosphate concentrate powder deposited below.
PUM
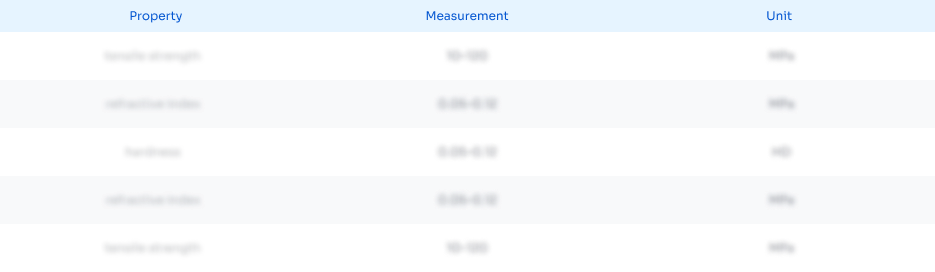
Abstract
Description
Claims
Application Information

- R&D Engineer
- R&D Manager
- IP Professional
- Industry Leading Data Capabilities
- Powerful AI technology
- Patent DNA Extraction
Browse by: Latest US Patents, China's latest patents, Technical Efficacy Thesaurus, Application Domain, Technology Topic, Popular Technical Reports.
© 2024 PatSnap. All rights reserved.Legal|Privacy policy|Modern Slavery Act Transparency Statement|Sitemap|About US| Contact US: help@patsnap.com