Cross-shaped ultrasonic array sensor and method for transformer partial discharge localization
An array sensor, ultrasonic array technology, applied in fault location, testing dielectric strength and other directions, can solve the problems of large cross-sectional area, difficult layout and high cost of array sensors
- Summary
- Abstract
- Description
- Claims
- Application Information
AI Technical Summary
Problems solved by technology
Method used
Image
Examples
Embodiment Construction
[0017] Virtually expand the original cross-shaped array by using high-order cumulant processing technology, and establish a mathematical model of the cross-shaped ultrasonic array. The array elements are located on the X and Y axes and arranged at equal intervals. Point P is the partial discharge position, and θ and Represent the pitch angle and azimuth angle of the incoming wave direction, respectively. The coordinates of the virtual array elements can be obtained by subtracting the coordinates of each array element from each other. The positions before and after expansion are as follows: figure 2 As shown, the solid circle is the actual array element position, and the hollow circle is the virtual array element position. Depend on figure 2 It can be seen that the expanded array elements are planar arrays.
[0018] The steps of using the extended array to locate the partial discharge are: calculating the fourth-order cumulant matrix Rcum of the ultrasonic signal received ...
PUM
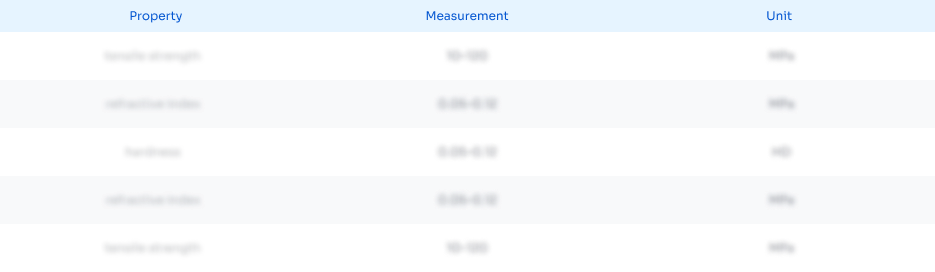
Abstract
Description
Claims
Application Information

- R&D
- Intellectual Property
- Life Sciences
- Materials
- Tech Scout
- Unparalleled Data Quality
- Higher Quality Content
- 60% Fewer Hallucinations
Browse by: Latest US Patents, China's latest patents, Technical Efficacy Thesaurus, Application Domain, Technology Topic, Popular Technical Reports.
© 2025 PatSnap. All rights reserved.Legal|Privacy policy|Modern Slavery Act Transparency Statement|Sitemap|About US| Contact US: help@patsnap.com