Fully CNC Camshaft Milling Machine
A camshaft and milling machine technology, which is applied to milling machine equipment, milling machine equipment details, driving devices, etc., can solve the problems of increasing the processing cost of camshafts, reducing production efficiency, and increasing the area of the workshop, saving materials and processing man-hours, The effect of reducing manufacturing costs and reducing work area
- Summary
- Abstract
- Description
- Claims
- Application Information
AI Technical Summary
Problems solved by technology
Method used
Image
Examples
Embodiment Construction
[0014] in figure 1 , figure 2 with image 3 Wherein, the full numerical control camshaft milling machine includes a bed 9, a guide rail plate 10, a guide rail 19, a rotary power head 6, a milling power head 3, a column 14, a main motor 2, a servo motor Ⅰ 7, a servo motor Ⅱ 17, a lifting table 20 and Lifting power head 16, the guide rail plate and the guide rail are arranged side by side on the bed, the guide rail is in the front, the guide rail is in the back, and the two ends of the guide plate are respectively provided with a rotary power head 6, which is directly driven by a servo motor I7, The synchronous transmission is controlled by a full numerical control system. The rotary power head is provided with a hydraulic chuck 11 that can clamp the camshaft 12, and five auxiliary supports 8 that can support the camshaft horizontally are arranged at intervals between the hydraulic chucks. The number of settings can be determined according to the length and size of the camshaft....
PUM
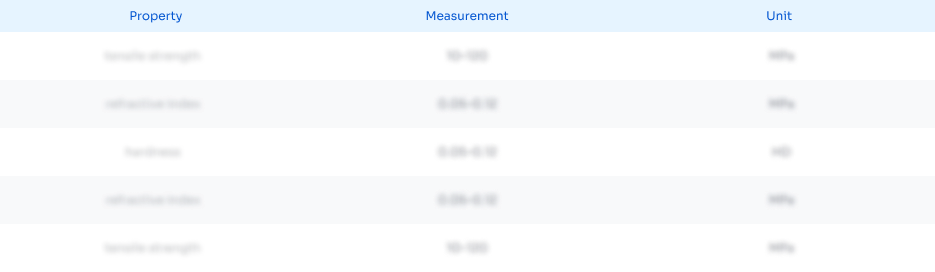
Abstract
Description
Claims
Application Information

- R&D
- Intellectual Property
- Life Sciences
- Materials
- Tech Scout
- Unparalleled Data Quality
- Higher Quality Content
- 60% Fewer Hallucinations
Browse by: Latest US Patents, China's latest patents, Technical Efficacy Thesaurus, Application Domain, Technology Topic, Popular Technical Reports.
© 2025 PatSnap. All rights reserved.Legal|Privacy policy|Modern Slavery Act Transparency Statement|Sitemap|About US| Contact US: help@patsnap.com