A quasi-distributed composite structure strain and temperature detection system
A composite material, quasi-distributed technology, used in thermometers, thermometers, measuring devices and other directions with physical/chemical changes, can solve the problems of large measurement errors, low signal-to-noise ratio, difficult remote monitoring, etc., to achieve convenient and feasible production. , The technological level is mature, the effect of prolonging the light time
- Summary
- Abstract
- Description
- Claims
- Application Information
AI Technical Summary
Problems solved by technology
Method used
Image
Examples
Embodiment Construction
[0020] The present invention will be further explained below in conjunction with specific embodiments. It should be understood that these embodiments are only used to illustrate the present invention and not to limit the scope of the present invention. In addition, it should be understood that after reading the teachings of the present invention, those skilled in the art can make various changes or modifications to the present invention, and these equivalent forms also fall within the scope defined by the appended claims of this application.
[0021] The embodiment of the present invention relates to a quasi-distributed composite material structure strain and temperature detection system, such as figure 1 As shown, including broadband light source 1, fiber isolator 2, 2×2 fiber coupler 3, index matching liquid 4, 1×m optical switch 5, m×n network fiber grating sensor head 6, fiber adjustable FP The filter 7, the photoelectric conversion module 8, the signal amplifier 9, the data ...
PUM
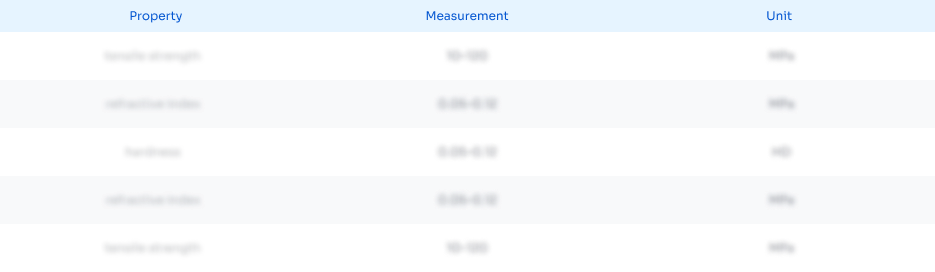
Abstract
Description
Claims
Application Information

- R&D
- Intellectual Property
- Life Sciences
- Materials
- Tech Scout
- Unparalleled Data Quality
- Higher Quality Content
- 60% Fewer Hallucinations
Browse by: Latest US Patents, China's latest patents, Technical Efficacy Thesaurus, Application Domain, Technology Topic, Popular Technical Reports.
© 2025 PatSnap. All rights reserved.Legal|Privacy policy|Modern Slavery Act Transparency Statement|Sitemap|About US| Contact US: help@patsnap.com