Method for producing wire drawing woven bag by adopting discarded plastic one-step method
A technology of waste plastics and production methods, which is applied in the direction of melt spinning, filament forming treatment, filament/thread forming, etc., can solve problems such as increased labor costs, high heating energy consumption, and poor product quality, so as to improve quality and The effect of product quality, labor saving and low production cost
- Summary
- Abstract
- Description
- Claims
- Application Information
AI Technical Summary
Problems solved by technology
Method used
Examples
Embodiment Construction
[0015] A one-step method for producing wire-drawn woven bags of waste plastics. The specific method is to integrate the crushing system and the cleaning system into a production line, and send the pre-sorted waste plastics into the crushing system from the conveyor device, and the silk materials directly enter the friction cleaning machine after they come out. , The silk material is spirally rotated through the closed loop circulating high-pressure water of the friction washing machine. After the initial flushing and sieving of the sediment, the friction softens the material and enters the rinsing pool. After rinsing to settle the dense sundries, they are sent to the mixing bin by the conveyor belt, stacked and filtered, and then sent to the next production unit
[0016] Then use the air duct to send the warehouse raw materials into the mixing chamber according to the molecular structure and solubility index of different waste plastics, and mix them with masterbatches, colorant...
PUM
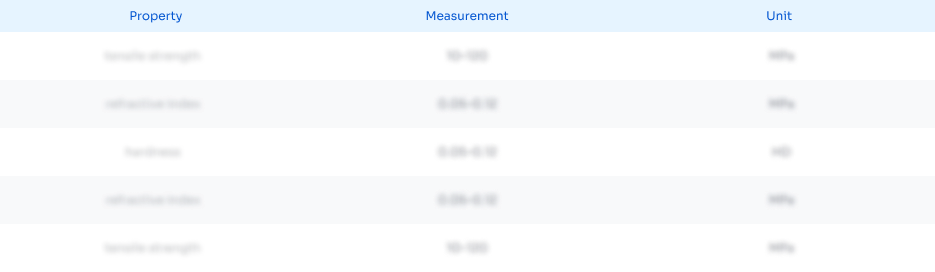
Abstract
Description
Claims
Application Information

- R&D
- Intellectual Property
- Life Sciences
- Materials
- Tech Scout
- Unparalleled Data Quality
- Higher Quality Content
- 60% Fewer Hallucinations
Browse by: Latest US Patents, China's latest patents, Technical Efficacy Thesaurus, Application Domain, Technology Topic, Popular Technical Reports.
© 2025 PatSnap. All rights reserved.Legal|Privacy policy|Modern Slavery Act Transparency Statement|Sitemap|About US| Contact US: help@patsnap.com