Method for producing gasoline blended component with high octane number from refinery gas and light hydrocarbons
A high-octane gasoline and refinery gas technology, applied in the field of aromatization of light hydrocarbons, can solve problems such as high processing costs, unreasonable system flow, and insufficient reaction depth, achieve good economic and social benefits, and reduce development The effect of increasing the number of downtime and increasing the overall profit
- Summary
- Abstract
- Description
- Claims
- Application Information
AI Technical Summary
Problems solved by technology
Method used
Image
Examples
Embodiment Construction
[0029] like figure 1 As shown, after the light hydrocarbon component is pressurized by the light hydrocarbon component feed pump 1, a part is mixed with the gasoline pressurized by the gasoline feed pump 16, and the mixed raw material is divided into two paths and passed through the first reaction product heat exchanger 2 ( or the second reaction product heat exchanger 15), the first reaction product heat exchanger 4 (or the second reaction product heat exchanger 15), and the first heating furnace 3 (or the second heating furnace 13) are heated to 320-420° C. Enter the first reactor 5 (or the second reactor 12) to react; after the other part is vaporized by the heating vaporizer 17, then enter the second and third sections of the first reactor 5 (or the second reactor 12), It is used to adjust the inlet temperature of the bed. The reaction product comes out from the first reactor 5 (the second reactor 12), through the first reaction heat exchanger 2, the first reaction produc...
PUM
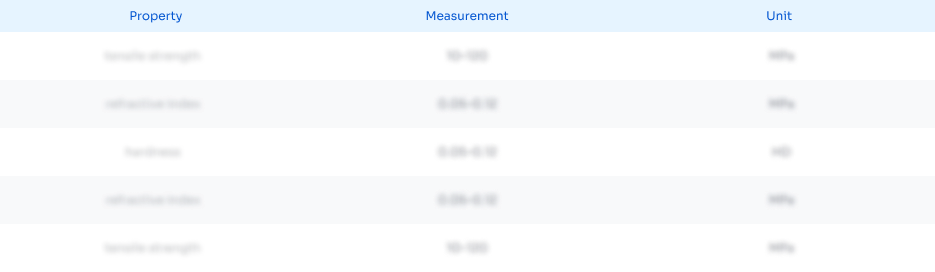
Abstract
Description
Claims
Application Information

- R&D
- Intellectual Property
- Life Sciences
- Materials
- Tech Scout
- Unparalleled Data Quality
- Higher Quality Content
- 60% Fewer Hallucinations
Browse by: Latest US Patents, China's latest patents, Technical Efficacy Thesaurus, Application Domain, Technology Topic, Popular Technical Reports.
© 2025 PatSnap. All rights reserved.Legal|Privacy policy|Modern Slavery Act Transparency Statement|Sitemap|About US| Contact US: help@patsnap.com