Method for controlling CO/H2 molar ratio in coal to methanol purification device
A purification device and coal-to-methanol technology, applied in chemical instruments and methods, inorganic chemistry, non-metallic elements, etc., can solve the problem of catalyst bed temperature, reactive CO transformation reaction degree difficult to control, large loading amount, and impossible to optimize Methanol circulation system and other issues, to achieve the effects of stable operation and operation control, avoiding large fluctuations in CO content, and facilitating the use of heat
- Summary
- Abstract
- Description
- Claims
- Application Information
AI Technical Summary
Problems solved by technology
Method used
Image
Examples
Embodiment Construction
[0022] The present invention will be further described in detail below in conjunction with the accompanying drawings and embodiments.
[0023] Such as figure 1 and figure 2 As shown, the CO / H 2 The method of molar ratio is as follows:
[0024] 1. Crude syngas split, CO conversion, two-way syngas heat exchange, the specific steps are as follows:
[0025] The crude synthesis gas from the gasification unit at a temperature of 240°C and a pressure of 62 barg has a molar composition of H 2 O: 58.55%, H 2 : 15.19%, CO: 18.28%, CO 2 : 7.63%, H 2 S: 0.106%, others: 0.244%; the gas-liquid separator 1 at the inlet of the crude synthesis gas sent to the CO conversion unit separates the liquid phase, and the obtained gas phase is divided into two paths, namely, the first synthesis gas and the second Synthetic gas. The flow ratio of the first synthesis gas and the second synthesis gas changes according to different processes: for example, in the process of coal water slurry gasifi...
PUM
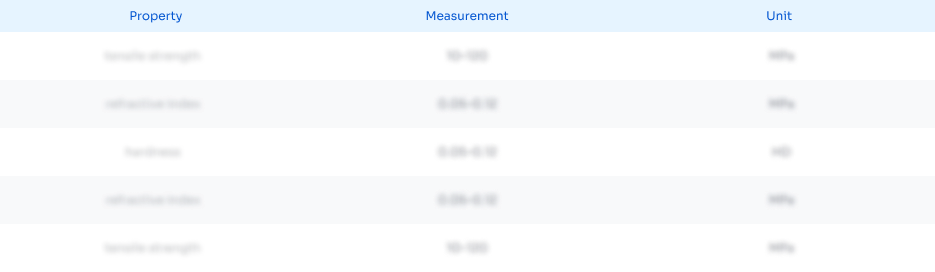
Abstract
Description
Claims
Application Information

- R&D Engineer
- R&D Manager
- IP Professional
- Industry Leading Data Capabilities
- Powerful AI technology
- Patent DNA Extraction
Browse by: Latest US Patents, China's latest patents, Technical Efficacy Thesaurus, Application Domain, Technology Topic, Popular Technical Reports.
© 2024 PatSnap. All rights reserved.Legal|Privacy policy|Modern Slavery Act Transparency Statement|Sitemap|About US| Contact US: help@patsnap.com