Method of monolithic photo-voltaic module assembly
A photovoltaic and laser technology, used in photovoltaic power generation, laser welding equipment, electrical components, etc., can solve the problem that the electrical connection state is not well defined.
- Summary
- Abstract
- Description
- Claims
- Application Information
AI Technical Summary
Problems solved by technology
Method used
Image
Examples
Embodiment Construction
[0024] figure 1 An overview of the different layers in the structure of a back contact solar cell module laminate 1 is shown. From bottom to top, the laminate 1 comprises or consists of: a conductive substrate 2, a first encapsulant layer 3 perforated on the rear side, a back contact solar cell 4, a second encapsulant layer 5 on top and of glass plates6. These layers are placed sequentially through the assembly process.
[0025] The conductive substrate 2 may be of any type such as tedlar-PET-copper, tedlar-PET-aluminium, but also on alternative structures such as glass-based PET, epoxy resin Base PET, or coated PET, etc. In an embodiment, the conductive substrate is constructed by a stack of layers comprising: at least one layer having a mechanical rigidity function, such as a PET layer, a glass layer, a fiber reinforced epoxy layer, etc.; at least one layer having a UV blocking function (such as a Tedlar layer, a PVDF layer, etc.); and at least one layer having a conduct...
PUM
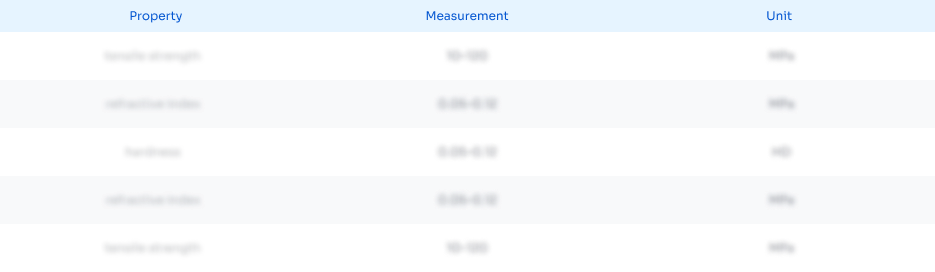
Abstract
Description
Claims
Application Information

- R&D
- Intellectual Property
- Life Sciences
- Materials
- Tech Scout
- Unparalleled Data Quality
- Higher Quality Content
- 60% Fewer Hallucinations
Browse by: Latest US Patents, China's latest patents, Technical Efficacy Thesaurus, Application Domain, Technology Topic, Popular Technical Reports.
© 2025 PatSnap. All rights reserved.Legal|Privacy policy|Modern Slavery Act Transparency Statement|Sitemap|About US| Contact US: help@patsnap.com