Roll-welded pipe spiral electroplating equipment and electroplating method thereof
A kind of electroplating equipment and spiral technology, which is applied in the spiral electroplating equipment and its electroplating field of welded pipe, can solve the problems that the electroplating equipment occupies an area, the current is different, and the electroplating effect is not good, so as to improve the electroplating efficiency , save equipment cost, the effect of consistent current size
- Summary
- Abstract
- Description
- Claims
- Application Information
AI Technical Summary
Problems solved by technology
Method used
Image
Examples
Embodiment
[0022] Such as figure 1 The spiral electroplating equipment for coiled welded pipe shown is provided with a drum 1 in the electroplating tank, and the ratio of the outer diameter of the drum 1 to the outer diameter of the rough rolled welded pipe is 100:1; the drum is provided with a surrounding track 2, so that The rough rolled welded pipe can be spirally wound on the drum along the orbit 2 for electroplating; there are also several power supply points 3 on the drum, and the distance between the power supply points 3 is 50 times the outer diameter of the rough rolled welded pipe.
[0023] working principle:
[0024] In the present invention, by setting a surrounding track on the drum, before electroplating, the rough rolled welded pipe is helically wound on the drum along the surrounding track, and then put into the electroplating tank for electroplating, and the drum is rotated according to the electroplating progress, so that the electroplated welded pipe is continuously fr...
PUM
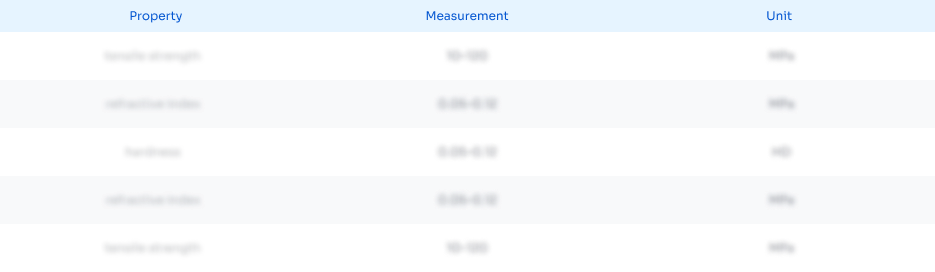
Abstract
Description
Claims
Application Information

- Generate Ideas
- Intellectual Property
- Life Sciences
- Materials
- Tech Scout
- Unparalleled Data Quality
- Higher Quality Content
- 60% Fewer Hallucinations
Browse by: Latest US Patents, China's latest patents, Technical Efficacy Thesaurus, Application Domain, Technology Topic, Popular Technical Reports.
© 2025 PatSnap. All rights reserved.Legal|Privacy policy|Modern Slavery Act Transparency Statement|Sitemap|About US| Contact US: help@patsnap.com