Gating system for stamping cylinder
A pouring system and cylinder technology, applied in the field of foundry processing, can solve the problems of secondary oxidation of molten iron, splash of molten iron, large drop between upper and lower sides, etc., and achieve the effect of preventing secondary oxidation and stable pouring
- Summary
- Abstract
- Description
- Claims
- Application Information
AI Technical Summary
Problems solved by technology
Method used
Image
Examples
Embodiment Construction
[0028] The following are preferred embodiments of the present invention, but are not intended to limit the protection scope of the present invention.
[0029] refer to figure 1 As shown, a pouring system for a stamping cylinder, which includes a sprue basin 1, a sprue 2, an upper runner 3, a lower runner 4, an inner sprue 5, The sand mold 6 is composed of a sand mold and a mold cavity. The sprue 2 is divided into at least two buffer sprues, and a first buffer runner 10 is arranged between adjacent buffer sprues.
[0030] It also includes a transition upper runner 7 and a transition lower runner 8 located between the sprue 2 and the upper runner 3, and the transition upper runner 7 and the transition lower runner 8 are provided There is filter brick 9 for filtering molten iron scum.
[0031] The ingate channel 5 is a "U" elbow, and the outlet of the "U" elbow molten iron is connected to the cavity of the sand mold 6 and is arranged vertically upward.
[0032] The sprue 2 is ...
PUM
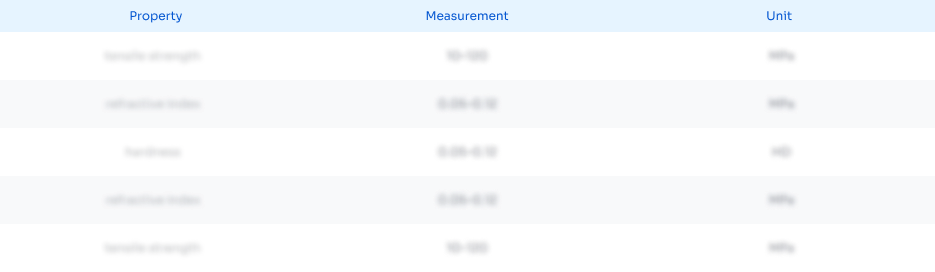
Abstract
Description
Claims
Application Information

- Generate Ideas
- Intellectual Property
- Life Sciences
- Materials
- Tech Scout
- Unparalleled Data Quality
- Higher Quality Content
- 60% Fewer Hallucinations
Browse by: Latest US Patents, China's latest patents, Technical Efficacy Thesaurus, Application Domain, Technology Topic, Popular Technical Reports.
© 2025 PatSnap. All rights reserved.Legal|Privacy policy|Modern Slavery Act Transparency Statement|Sitemap|About US| Contact US: help@patsnap.com