Method for preparing K438 alloy by adopting K438 alloy return material
A technology for returning materials and alloys, applied in the direction of improving process efficiency and improving energy efficiency, can solve problems such as waste of precious metals, and achieve the effects of strong applicability, reduction of production costs, and improvement of material utilization rate.
- Summary
- Abstract
- Description
- Claims
- Application Information
AI Technical Summary
Problems solved by technology
Method used
Image
Examples
Embodiment Construction
[0018] A kind of preparation method that adopts K438 alloy return material to prepare K438 alloy, comprises the steps:
[0019] (1) Purification treatment of K438 alloy return material: first, carry out tumbling treatment on the return material, and the time of tumbling treatment is 8 hours, then perform sand blasting on the surface of the return material, and then use compressed air to blow the The surface of the returned material is blown clean;
[0020] (2) The return material is smelted into the return material ingot: a 500kg vacuum induction melting furnace is used for melting, and the purified return material is loaded into the crucible of the melting furnace. Heating with electric power of 120kW for 25 minutes, and then heating with electric power of 200 for 12 minutes. After the surface of the returned material turns dark red, the melting furnace is heated with electric power of 240kW until all the returned materials are melted into a melt; use contact thermocouple or ...
PUM
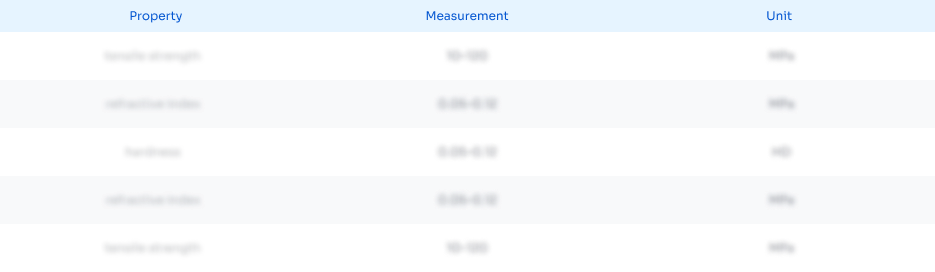
Abstract
Description
Claims
Application Information

- R&D Engineer
- R&D Manager
- IP Professional
- Industry Leading Data Capabilities
- Powerful AI technology
- Patent DNA Extraction
Browse by: Latest US Patents, China's latest patents, Technical Efficacy Thesaurus, Application Domain, Technology Topic, Popular Technical Reports.
© 2024 PatSnap. All rights reserved.Legal|Privacy policy|Modern Slavery Act Transparency Statement|Sitemap|About US| Contact US: help@patsnap.com