Composite casting system of crank shaft box
A crankcase body and casting system technology, applied in the direction of casting molds, casting mold components, casting molding equipment, etc., can solve the problems of large energy consumption, unstable slag blocking effect, long production cycle, etc., to reduce casting costs and improve Good production efficiency and slag blocking effect
- Summary
- Abstract
- Description
- Claims
- Application Information
AI Technical Summary
Problems solved by technology
Method used
Image
Examples
Embodiment Construction
[0027] The present invention is further described below by embodiment, and present embodiment is only used for further description of the present invention, but can not be interpreted as the limitation of protection scope of the present invention, those skilled in the art makes some non-essential claims according to the content of the present invention Improvements and adjustments belong to the protection scope of the present invention.
[0028] combine figure 1 to map Figure 5 .
[0029] As shown in the figure, the composite casting system for the crankcase body includes the bottom plate core for fitting and positioning, the water jacket core and the main core that form the crankcase structure with each core, the end face cores located at both ends of the main core, and the cores located on both sides of the main core. The outer core and the upper gating system, base plate core, water jacket core, main core, and gating system are sequentially stacked from the bottom to the...
PUM
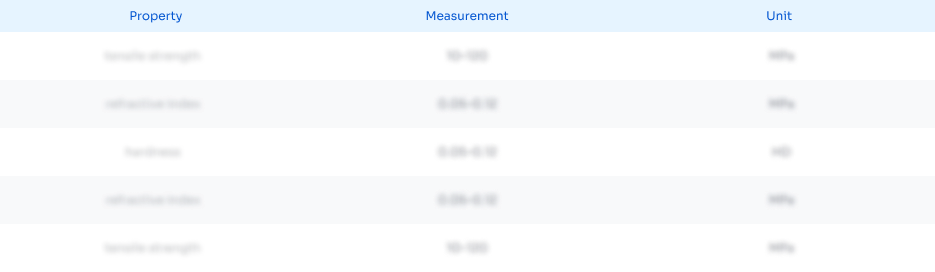
Abstract
Description
Claims
Application Information

- R&D Engineer
- R&D Manager
- IP Professional
- Industry Leading Data Capabilities
- Powerful AI technology
- Patent DNA Extraction
Browse by: Latest US Patents, China's latest patents, Technical Efficacy Thesaurus, Application Domain, Technology Topic, Popular Technical Reports.
© 2024 PatSnap. All rights reserved.Legal|Privacy policy|Modern Slavery Act Transparency Statement|Sitemap|About US| Contact US: help@patsnap.com