Cu/CeOx-TiO2 for selective catalytic oxidization of ammonia and preparation method thereof
A catalytic oxidation and catalyst technology, applied in catalyst activation/preparation, metal/metal oxide/metal hydroxide catalyst, physical/chemical process catalyst, etc., can solve the problems of low temperature activity and low selectivity of catalyst, and achieve oxidation The effect of enhanced reducing activity, high N2 selectivity, and good low temperature activity
- Summary
- Abstract
- Description
- Claims
- Application Information
AI Technical Summary
Problems solved by technology
Method used
Examples
Embodiment 1
[0023] Example 1, Cu / CeO x -TiO 2 Preparation of catalysts and their properties.
[0024] In the first step, the additive CeO was impregnated x added to TiO 2in solid powder
[0025] 0.217g solid Ce(NO 3 ) 3 ·6H 2 O was dissolved in 50ml of water, and then 2g of powdered TiO 2 impregnated in Ce(NO 3 ) 3 solution, so that the molar ratio of Ce to Ti was 1 / 50, then dried at 60°C for 6h, then heated to 300°C in a muffle furnace, calcined for 4h, and finally cooled to room temperature to obtain the oxide CeO x -TiO 2 .
[0026] The second step is to use the homogeneous precipitation method to load the active component copper
[0027] 0.06g solid Cu(NO 3 ) 2 Dissolve in 10ml water, then take 2g of the solid oxide CeO prepared in the first step x -TiO 2 Added to the copper nitrate solution, so that the solid Cu(NO 3 ) 2 with solid oxide CeO x -TiO 2 The mass ratio of the mixed solution is 0.03:1. The mixed solution is magnetically stirred at 60°C. During the stir...
Embodiment 2
[0030] Example 2, Cu / CeO x -TiO 2 Preparation of catalysts and their properties.
[0031] In the first step, the additive CeO was impregnated x added to TiO 2 in solid powder
[0032] 54.25gCe(NO 3 ) 3 ·6H 2 O was dissolved in 500ml of water, and then 50g of powdered TiO 2 impregnated in Ce(NO 3 ) 3 solution, so that the molar ratio of Ce to Ti is 1 / 5, and then dried at 120°C for 16h, then heated to 600°C in a muffle furnace, calcined for 2h, and finally lowered to room temperature to obtain the oxide CeO x -TiO 2 .
[0033] The second step is to use the homogeneous precipitation method to load the active component copper
[0034] 88.2g solid Cu(NO 3 ) 2 Dissolve in 10ml water, then take 70g of the solid oxide CeO prepared in the first step x -TiO 2 Added to the copper nitrate solution, so that the solid Cu(NO 3 ) 2 with solid oxide CeO x -TiO 2 The mass ratio is 1.26:1. The mixed solution was magnetically stirred at 120°C, and urea with a concentration of...
Embodiment 3
[0037] Example 3, Cu / CeO x -TiO 2 Preparation of catalysts and their properties.
[0038] In the first step, the additive CeO was impregnated x added to TiO 2 in solid powder
[0039] 1.81gCe(NO 3 ) 3 ·6H 2 O was dissolved in 100ml of water, and then 10g of powdered TiO 2 impregnated in Ce(NO 3 ) 3 In the solution, the molar ratio of Ce to Ti was 1 / 30, then dried at 90°C for 10h, then heated to 400°C in a muffle furnace, calcined for 3h, and finally, cooled to room temperature to obtain the oxide CeO x -TiO 2 .
[0040] The second step is to use the homogeneous precipitation method to load the active component copper
[0041] 6.8g of solid Cu(NO 3 ) 2 ·3H 2 O is dissolved in 10ml of water, then take 10g of the solid oxide CeO prepared in the first step x -TiO 2 Dissolved in the copper nitrate solution, so that solid Cu(NO 3 ) 2 ·3H 2 O and solid oxide CeO x -TiO 2 The mass ratio is 0.68:1. The mixed solution was magnetically stirred at 90°C. During stirr...
PUM
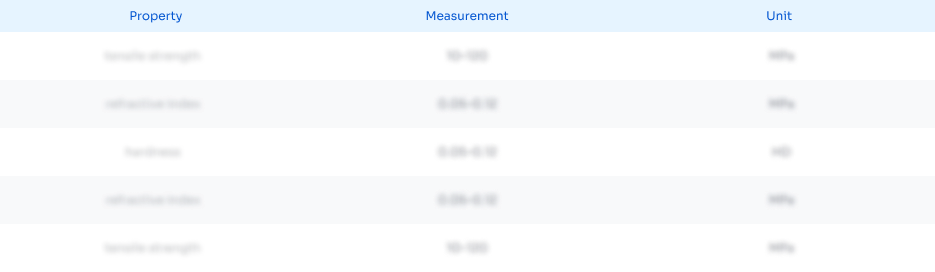
Abstract
Description
Claims
Application Information

- R&D
- Intellectual Property
- Life Sciences
- Materials
- Tech Scout
- Unparalleled Data Quality
- Higher Quality Content
- 60% Fewer Hallucinations
Browse by: Latest US Patents, China's latest patents, Technical Efficacy Thesaurus, Application Domain, Technology Topic, Popular Technical Reports.
© 2025 PatSnap. All rights reserved.Legal|Privacy policy|Modern Slavery Act Transparency Statement|Sitemap|About US| Contact US: help@patsnap.com