Gold colored metallic pigments that include manganese oxide nanoparticles layers
A nano-particle, manganese oxide technology, applied in the field of coating pigments, can solve the problems of separation of yellow pigments and aluminum flakes, loss of gold color, inconsistent color, etc.
- Summary
- Abstract
- Description
- Claims
- Application Information
AI Technical Summary
Problems solved by technology
Method used
Image
Examples
example 1
[0096] Step 1 Silicon passivation: To a 2L reaction flask equipped with a stirrer and condenser was added the following chemicals: 1.133g aluminum flakes (Sparkle Premium 695, 100 g aluminum metal equivalent), 600 g propylene glycol methyl ether; 2.30 g tetraethyl orthosilicate; 3.20 ml 28% ammonia solution; the mixture was continuously stirred at 85° C. for 6 hours. Once the reaction time had elapsed, the mixture was vacuum filtered and rinsed with propylene glycol methyl ether.
[0097] Step 2 Aminosilane Anchor Group Immobilization To a 2L reaction flask was added the following chemicals: 1.125g silicon passivated aluminum flakes (90g aluminum metal equivalent); 2.500g propylene glycol methyl ether; 3.20mL N-[3-(methoxy 4.20 mL of deionized water; the mixture was continuously stirred for 2 hours at 25° C. Once the reaction time was over, the mixture was filtered and rinsed with propylene glycol methyl ether.
[0098] Step 3 MnO 2 Nanoparticle Deposition To a 2 L reaction...
example 2
[0102] Step 1 Silicon passivation: To a 2L reaction flask equipped with a stirrer and condenser was added the following chemicals: 1.133g aluminum flakes (Sparkle Premium 695, 100 g aluminum metal equivalent), 600 g propylene glycol methyl ether; 2.30 g tetraethyl orthosilicate; 3.20 mL 28% ammonia solution; the mixture was continuously stirred at 85° C. for 6 hours. Once the reaction time had elapsed, the mixture was vacuum filtered and rinsed with propylene glycol methyl ether.
[0103]Step 2 Aminosilane anchoring group immobilization: Add the following chemicals to a 2L reaction flask: 1.125g silicon-passivated aluminum flakes (90g aluminum metal equivalent); 2.500g propylene glycol methyl ether; 3.20mL N-[3-(trimethoxy Trimthoxylsilyl)propyl]-ethylenediamine; 4.20 mL of deionized water; the mixture was continuously stirred at 25° C. for 2 hours. Once the reaction time was over, the mixture was filtered and rinsed with propylene glycol methyl ether.
example 4
[0106] To a 2L reaction flask equipped with a stirrer and condenser was added the following chemicals: 1. 96g golden metallic pigment (50g solid, 39g aluminum metal equivalent) prepared from Example 2; 2.250g propylene glycol methyl ether; 3.8g orthosilicate Ethyl ester; 4.4 mL of 28% aqueous ammonia solution; the mixture was continuously stirred at 85°C for 6 hours. Once the reaction time had elapsed, the mixture was vacuum filtered and rinsed with propylene glycol methyl ether. Example 5
PUM
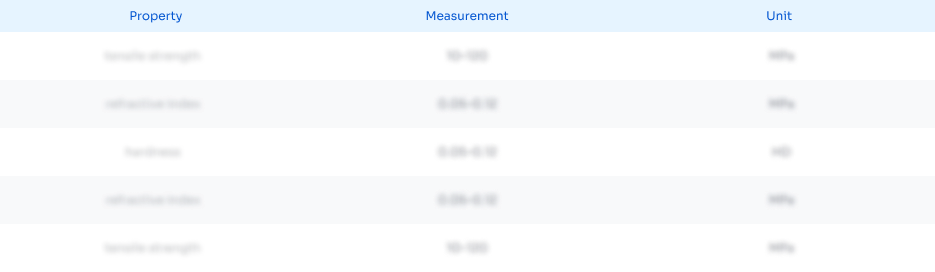
Abstract
Description
Claims
Application Information

- R&D
- Intellectual Property
- Life Sciences
- Materials
- Tech Scout
- Unparalleled Data Quality
- Higher Quality Content
- 60% Fewer Hallucinations
Browse by: Latest US Patents, China's latest patents, Technical Efficacy Thesaurus, Application Domain, Technology Topic, Popular Technical Reports.
© 2025 PatSnap. All rights reserved.Legal|Privacy policy|Modern Slavery Act Transparency Statement|Sitemap|About US| Contact US: help@patsnap.com