Brake energy feedback control method of pure electric automobile
A braking energy feedback, pure electric vehicle technology, applied in electric vehicles, electric braking systems, vehicle components, etc., can solve problems such as difficulty in obtaining satisfactory results, inability to actively avoid vehicle jitter, and inability to lock wheels
- Summary
- Abstract
- Description
- Claims
- Application Information
AI Technical Summary
Problems solved by technology
Method used
Image
Examples
Embodiment Construction
[0034] The utility model will be described in further detail below through specific embodiments in conjunction with the accompanying drawings.
[0035] Such as figure 1 The schematic diagram of regenerative braking with braking energy feedback is shown. Generally speaking, the voltage generated by the braking energy regenerative power generation system is always lower than the battery voltage, so in order to charge the electric energy generated by the braking energy regenerative power generation system into the battery, a special control system must be adopted to make the motor work in regenerative braking mode . The principle of braking energy feedback regenerative braking is as follows: figure 1 shown. in the picture is the resistance, is the braking current limiting resistor, is the battery voltage, is the induced potential of the motor, and L is the inductance of the motor armature. When working, the drive current of the motor armature is disconnected, and the ...
PUM
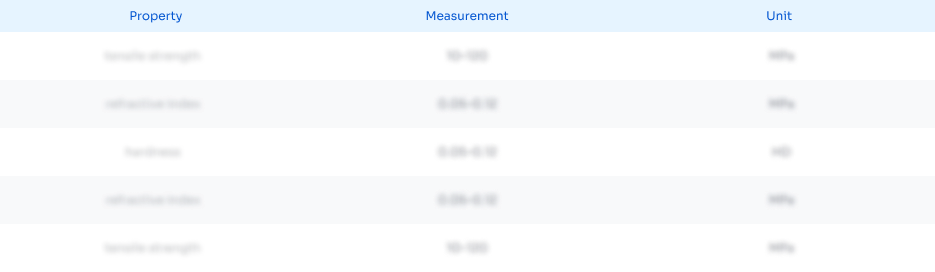
Abstract
Description
Claims
Application Information

- R&D
- Intellectual Property
- Life Sciences
- Materials
- Tech Scout
- Unparalleled Data Quality
- Higher Quality Content
- 60% Fewer Hallucinations
Browse by: Latest US Patents, China's latest patents, Technical Efficacy Thesaurus, Application Domain, Technology Topic, Popular Technical Reports.
© 2025 PatSnap. All rights reserved.Legal|Privacy policy|Modern Slavery Act Transparency Statement|Sitemap|About US| Contact US: help@patsnap.com