Rotary ultrasonic head based on machine tool attachment
An ultrasonic head and machine tool technology, applied in the direction of tool clamps, etc., can solve the problems of speed limit, poor interchangeability, wear or damage, etc., to meet the needs of high-power processing, good versatility and interchangeability, and improved induction efficiency. Effect
- Summary
- Abstract
- Description
- Claims
- Application Information
AI Technical Summary
Problems solved by technology
Method used
Image
Examples
Embodiment 1
[0087] Figure 11 It shows the structure of Embodiment 1 of a rotary ultrasonic head based on the machine tool attachment of the present invention. The main components include an ultrasonic vibration working device, a non-contact collector ring, a main shaft 17, a tool handle 16, a support shell 12, and a shift fork 13. The first bearing 11, the second bearing 14, the main side insulating cage 22 of the collector ring, and the secondary side insulating cage 23 of the collector ring.
[0088] Some accessories are not shown among the figure, these accessories can be changed under the situation that the gist of the present invention remains unchanged.
[0089] One end of the main shaft 17 has an inner cavity D, and the inner cavity D is coaxial with the main shaft 17. Tool handle 16 is installed, the rotation axes of ultrasonic vibration working device (18, 9, 8, 7, 6), main shaft 17 and tool handle 16 are on the same straight line, and tool handle 16 is installed on the machine...
Embodiment 2
[0097] like Figure 12 Shown is the structure of Embodiment 2 of a rotary ultrasonic head based on machine tool attachment of the present invention, which is the same as Figure 11 The same parts of the illustrated embodiments will not be repeated, and only the differences will be described.
[0098] In the second example, the Figure 11 The split tool holder 16 and the main shaft 17 in the Figure 12The one-piece tool holder main shaft 24 shown in , that is, cancel the connecting part between the two under the premise that the respective functions of the tool holder and the main shaft remain unchanged, and manufacture the two as a whole. The one-piece tool holder main shaft 24 is due to the The handle and the main shaft are a whole and cannot be disassembled, that is, a rotating ultrasonic head corresponds to a certain type of tool handle, and can only be installed on the machine tool spindle that matches the type of tool handle. The interchangeability of the integrated typ...
Embodiment 3
[0100] like Figure 13 Shown is the structure of Embodiment 3 of a rotary ultrasonic head based on machine tool attachment of the present invention, which is the same as Figure 11 The same parts of the illustrated embodiments will not be repeated, and only the differences will be described.
[0101] Figure 13 The third embodiment shown does not have Figure 11 The first bearing 11 and the second bearing 14, the shift fork 13 and the accessories equipped for installing the bearings in the shown embodiment one, but the end of the support shell 12 close to the tool handle is directly fixedly connected with the machine tool bed, in this Under the premise that the purpose of the invention remains unchanged, the connection method can be that a magnetic seat (not shown in the figure) is set near the end of the support shell 12 near the handle of a knife, or use other connection methods. use Figure 13 In the third embodiment shown, the requirement for the coaxiality of the supp...
PUM
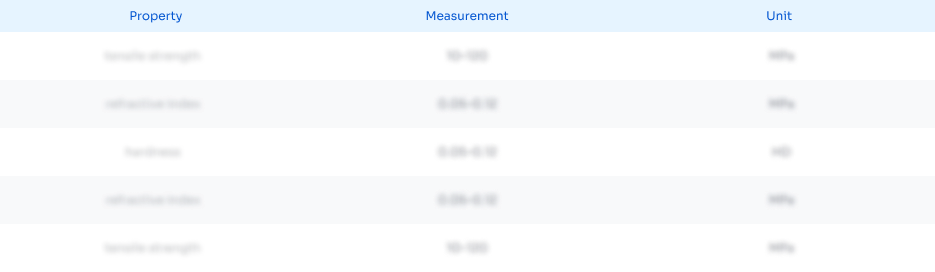
Abstract
Description
Claims
Application Information

- R&D
- Intellectual Property
- Life Sciences
- Materials
- Tech Scout
- Unparalleled Data Quality
- Higher Quality Content
- 60% Fewer Hallucinations
Browse by: Latest US Patents, China's latest patents, Technical Efficacy Thesaurus, Application Domain, Technology Topic, Popular Technical Reports.
© 2025 PatSnap. All rights reserved.Legal|Privacy policy|Modern Slavery Act Transparency Statement|Sitemap|About US| Contact US: help@patsnap.com