Method for preparing syringaldehyde by oxidative degradation of lignin
A technology of oxidative degradation and syringaldehyde, which is applied to the preparation of carbon-based compounds, chemical instruments and methods, and the preparation of organic compounds, can solve the problems of difficult separation and industrialization of oxidative degradation of lignin, and achieve cost reduction and high efficiency. The effect of value-added industrialization development and promoting the sustainable development of agriculture
- Summary
- Abstract
- Description
- Claims
- Application Information
AI Technical Summary
Problems solved by technology
Method used
Image
Examples
Embodiment 1
[0039] Put 2mol / L NaOH aqueous solution into the reaction kettle, add 60g / L lignocellulose enzymatic residue (Klasen lignin content is 40%), pass through 0.2Mpa nitrogen protection, start heating, after reaching the reaction temperature of 120°C , feed nitrogen to make the total pressure reach 1.5MPa, then quickly switch to oxygen, adjust the total pressure to 2.0Mpa, and start stirring at the same time, the stirring speed is 1000rpm, this time is set as the "zero point" of the reaction, and the reaction ends after 90min. The yield of vanillin was 11.5% (p-klasen lignin), the yield of syringaldehyde was 18.2% (p-lignin), and the yield of p-hydroxybenzaldehyde was 6.5% (p-klasen lignin).
[0040] After the reaction, the reaction solution was centrifuged at 4000 rpm and the centrifugation time was 2 minutes; the centrifuged solution was acidified with 20% sulfuric acid to a pH of about 2-3, precipitated overnight, filtered, and vacuum-dried at 50°C for 24 hours to obtain a yellow...
Embodiment 2
[0045] Put 3.0mol / L NaOH aqueous solution into the reactor, add 180g / L alkali lignin (Klasen lignin content is 90%), and drop 5g / L LaMn 0.7 Cu 0.3 o 3 Catalyst (self-made, preparation method is as follows: the required nitrate of molecular formula is dissolved in water and makes nitrate solution, adds citric acid and makes complexing agent solution in nitrate solution, the total amount of metal ions in citric acid and nitrate solution The molar ratio is 1: 1.5; the pH value of the complexing agent solution is adjusted to 5-6 by dripping ammonia water with a concentration of 10% in the complexing agent solution, and stirring and heating the complexing agent solution after adding the ammonia water to obtain wet condensation glue; the heating temperature is 80°C, the stirring speed is 200 rpm, and the stirring time is 8 hours). Introduce nitrogen protection of 0.1MPa, start heating, and after reaching 160°C, inject nitrogen to make the total pressure reach 2.0Mpa, then quickly ...
Embodiment 3
[0051] Put 0.2mol / L NaOH aqueous solution into the reactor, add 10g / L sulfonated lignin (Klasen lignin content is 92%), and put 100g / L CuO catalyst (chemically pure, purchased). Introduce nitrogen protection of 0.1MPa, start heating, after reaching 180°C, inject nitrogen to make the total pressure reach 2.0MPa, then quickly switch to oxygen, adjust the total pressure to 4.0Mpa, and start stirring at the same time, this time is defined as the "zero point of the reaction" ", the reaction ends after 30min. The yield of vanillin was 20.3%, the yield of syringaldehyde was 11.1%, and the yield of p-hydroxybenzaldehyde was 7.5%, all of which were calculated according to Klassen to lignin.
[0052] After the reaction, centrifuge the reaction liquid at 2000rpm and centrifuge for 10 minutes; add 20% sulfuric acid to the centrifuged liquid to acidify to a pH of about 2-3, precipitate overnight, filter, and vacuum-dry the precipitate at 50°C for 24 hours to obtain a yellow color solid. ...
PUM
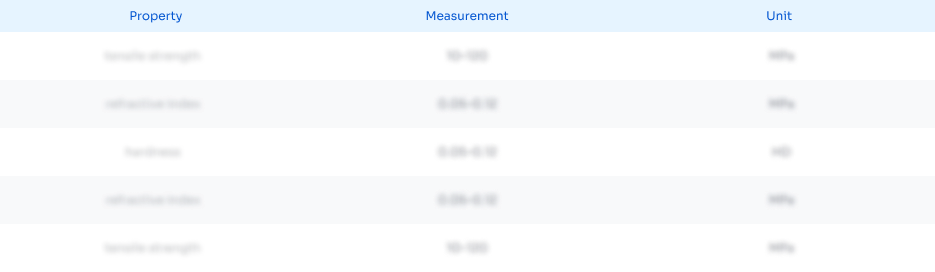
Abstract
Description
Claims
Application Information

- R&D Engineer
- R&D Manager
- IP Professional
- Industry Leading Data Capabilities
- Powerful AI technology
- Patent DNA Extraction
Browse by: Latest US Patents, China's latest patents, Technical Efficacy Thesaurus, Application Domain, Technology Topic, Popular Technical Reports.
© 2024 PatSnap. All rights reserved.Legal|Privacy policy|Modern Slavery Act Transparency Statement|Sitemap|About US| Contact US: help@patsnap.com