Horizontal retracing woven bag mouth and bottom sewer
A technology of bottom sewing machine and woven bag, which is applied in the direction of bag sewing machine, sewing unit, sewing equipment, etc., which can solve the problems of manpower occupation, high scrap rate, high price, etc., and achieve the reduction of equipment cost, lower scrap rate, and automation high effect
- Summary
- Abstract
- Description
- Claims
- Application Information
AI Technical Summary
Problems solved by technology
Method used
Image
Examples
Embodiment
[0012] The working steps of the horizontal fold-back woven bag sewing machine of the present invention are as follows:
[0013] The operator first puts the edge of the mouth of the braided tube into a corner and places it on the platform at the feed end of the seaming machine. The belt conveyor on the table of the seaming machine rolls in the braided tube and sends it to the sewing machine to sew the braided tube. The woven bag after the seam enters the transfer platform from the discharge end, and is positioned by the horizontal material baffle, and the sensor senses, and the horizontal transfer rubbing roller rotates to rub the woven bag to the left of the transfer platform. In order to prevent the woven bag from being skewed and turned, the wind feeder The two air outlets of the machine carry out wind force flattening on the upper part of the woven bag. When the woven bag enters the left side of the transfer platform, it is blocked and positioned by the longitudinal material...
PUM
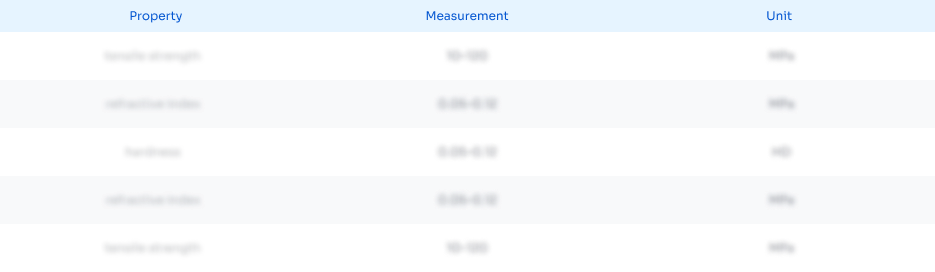
Abstract
Description
Claims
Application Information

- Generate Ideas
- Intellectual Property
- Life Sciences
- Materials
- Tech Scout
- Unparalleled Data Quality
- Higher Quality Content
- 60% Fewer Hallucinations
Browse by: Latest US Patents, China's latest patents, Technical Efficacy Thesaurus, Application Domain, Technology Topic, Popular Technical Reports.
© 2025 PatSnap. All rights reserved.Legal|Privacy policy|Modern Slavery Act Transparency Statement|Sitemap|About US| Contact US: help@patsnap.com