Method for separating cyclohexane and cyclohexene by extraction and rectification
A technology of extractive distillation and extractive distillation column, which is applied in the field of extractive distillation and separation, which can solve the problems of large reflux ratio and extractant feed ratio, energy consumption bottleneck, and difficult separation, so as to reduce the number of plates and reduce equipment investment. The effect of reduction and simple process flow
- Summary
- Abstract
- Description
- Claims
- Application Information
AI Technical Summary
Problems solved by technology
Method used
Image
Examples
Embodiment 1
[0026] Such as figure 1 As shown, 1 volume part of cyclohexane and cyclohexene mixed raw material liquid F2 is added into the tower from the middle and upper part of the extractive distillation tower 1, and 3 volume parts of the extractant sulfolane F1 with a purity of 99.0 wt% or more are passed through The heat exchanger 3 is heated to 80°C and added to the tower from the position near the top of the extractive distillation tower 1. The theoretical plate number of the extractive distillation tower 1 is 70, the operating pressure at the top of the tower is 30.0KPa, and the temperature at the top of the tower is It is 80 ℃, and the temperature of the tower bottom is 195 ℃, and the steam at the top of the tower is condensed and refluxed through the condenser 4, and the operating reflux ratio is 4.0: 1. The cyclohexane product D1 with a purity of 99.8wt% is extracted from the top of the tower, and the reboiler 5 Provide thermal power for the extractive distillation tower 1, the ...
Embodiment 2
[0029] Such as figure 1 As shown, 1 volume part of cyclohexane and cyclohexene mixed raw material liquid F2 is added into the tower from the middle and upper part of the extractive distillation tower 1, and the extraction agent sulfolane F1 with a purity of 2.5 volume parts above 99.0wt% is passed through The heat exchanger 3 is heated to 85°C and added to the tower from the position near the top of the extractive distillation tower 1. The theoretical plate number of the extractive distillation tower 1 is 75, the operating pressure at the top of the tower is 35.0KPa, and the temperature at the top of the tower is It is 84 ℃, and the temperature of the tower bottom is 199 ℃, and the steam at the top of the tower is condensed and refluxed through the condenser 4, and the operating reflux ratio is 5.0: 1. The cyclohexane product D1 with a purity of 99.7wt% is extracted from the top of the tower, and the reboiler 5 Provide thermal power for extractive distillation tower 1, the ric...
Embodiment 3
[0032] Such as figure 1As shown, 1 volume part of cyclohexane and cyclohexene mixed raw material liquid F2 is added into the tower from the middle and upper part of the extractive distillation tower 1, and the extraction agent sulfolane F1 with a purity of 2.7 volume parts above 99.0wt% is passed through The heat exchanger 3 is heated to 75°C and added to the tower from the position near the top of the extractive distillation tower 1. The theoretical plate number of the extractive distillation tower 1 is 65, the operating pressure at the top of the tower is 30.0KPa, and the temperature at the top of the tower is It is 75 ℃, and the temperature of the tower bottom is 190 ℃. The steam at the top of the tower is condensed and refluxed through the condenser 4. The operating reflux ratio is 5.0: 1. The cyclohexane product D1 with a purity of 99.6wt% is extracted from the top of the tower, and the reboiler 5 Provide thermal power for extractive distillation tower 1, the rich solvent...
PUM
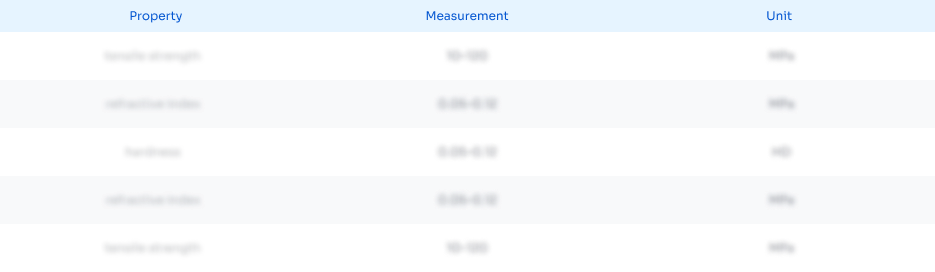
Abstract
Description
Claims
Application Information

- Generate Ideas
- Intellectual Property
- Life Sciences
- Materials
- Tech Scout
- Unparalleled Data Quality
- Higher Quality Content
- 60% Fewer Hallucinations
Browse by: Latest US Patents, China's latest patents, Technical Efficacy Thesaurus, Application Domain, Technology Topic, Popular Technical Reports.
© 2025 PatSnap. All rights reserved.Legal|Privacy policy|Modern Slavery Act Transparency Statement|Sitemap|About US| Contact US: help@patsnap.com