Manufacturing method of chip LED (light emitting diode) display screen
A technology of LED display screen and manufacturing method, which is applied to the parts of lighting devices, semiconductor devices of light-emitting elements, lighting and heating equipment, etc., which can solve the problems of poor antistatic ability, poor consistency, and low protection performance. Achieve stable performance, good display effect, and low power consumption
- Summary
- Abstract
- Description
- Claims
- Application Information
AI Technical Summary
Problems solved by technology
Method used
Image
Examples
Embodiment 1
[0039] Step 1. Mount-type high-brightness SMD LED lamp 1 and circuit board 2 are connected by welding, and the reverse side of circuit board 2 welded with SMD LED lamp 1 is treated with anti-adhesive protective film 3, see figure 1 and figure 2 ;
[0040] Step 2: Paste the anti-adhesive protective film 3. The processed circuit board 2 and the plastic injection mold 4 are locked by the screw 5, and the black waterproof colloid 7 with a hardness of 60 Shore D is injected into the plastic injection mold through the injection port 6. The liquid level of the waterproof colloid 7 is equal to the height of the top of the patch LED lamp. The waterproof colloid 7 contains anti-ultraviolet, anti-acid rain, and anti-reflection materials. , see image 3 and Figure 4 ;
[0041] Step 3, the excess colloid on the edge of the circuit board 2 filled with waterproof colloid 7 is cut off by a cutter 8, see Figure 5 and Image 6 ;
[0042] Step 4. The surface of the waterproof colloid b...
Embodiment 2
[0045] Step 1. Mount-type high-brightness SMD LED lamp 1 and circuit board 2 are connected by welding, and the reverse side of circuit board 2 welded with SMD LED lamp 1 is treated with anti-adhesive protective film 3, see figure 1 and figure 2 ;
[0046] Step 2: Paste the anti-adhesive protective film 3. The processed circuit board 2 and the plastic injection mold 4 are locked by the screw 5, and the black waterproof colloid 7 with a hardness of 80 Shore D is injected into the plastic injection mold through the injection port 6. The liquid level of the waterproof colloid 7 is equal to the height of the top of the patch LED lamp. The waterproof colloid 7 contains anti-ultraviolet, anti-acid rain, and anti-reflection materials. , see image 3 and Figure 4 ;
[0047] Step 3, the excess colloid on the edge of the circuit board 2 filled with waterproof colloid 7 is cut off by a cutter 8, see Figure 5 and Image 6 ;
[0048] Step 4. Cut out criss-cross deep grooves on the...
Embodiment 3
[0051] Step 1. Mount-type high-brightness SMD LED lamp 1 and circuit board 2 are connected by welding, and the reverse side of circuit board 2 welded with SMD LED lamp 1 is treated with anti-adhesive protective film 3, see figure 1 and figure 2 ;
[0052] Step 2, Paste the anti-adhesive protective film 3 The processed circuit board 2 and the injection mold 4 are tightened and assembled through the screw 5, and the black waterproof colloid 7 with a hardness of 65 Shore D is injected into the injection mold through the injection port 6. The liquid level of the waterproof colloid 7 is equal to the top of the patch LED lamp, and the waterproof colloid completely covers the circuit board. Due to the wall-climbing effect of the liquid, the waterproof colloid also covers the metal conductive pins of the patch LED lamp 1. At the same time, the LED and the A recessed area is formed between the LEDs;
[0053] Step 3, the excess colloid on the edge of the circuit board 2 filled with wat...
PUM
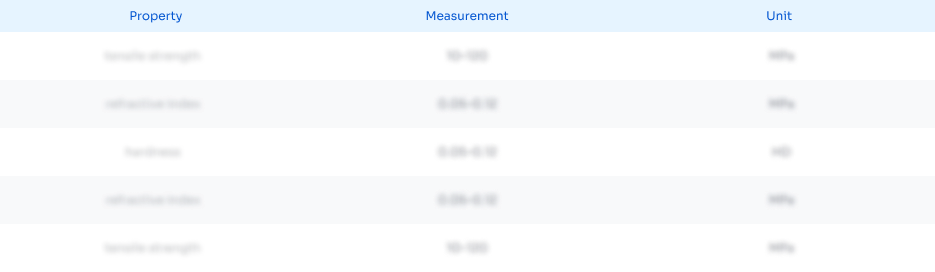
Abstract
Description
Claims
Application Information

- R&D Engineer
- R&D Manager
- IP Professional
- Industry Leading Data Capabilities
- Powerful AI technology
- Patent DNA Extraction
Browse by: Latest US Patents, China's latest patents, Technical Efficacy Thesaurus, Application Domain, Technology Topic, Popular Technical Reports.
© 2024 PatSnap. All rights reserved.Legal|Privacy policy|Modern Slavery Act Transparency Statement|Sitemap|About US| Contact US: help@patsnap.com