Microchannel heat exchanger
A micro-channel heat exchanger and micro-channel technology, applied in evaporator/condenser, lighting and heating equipment, refrigeration components, etc., can solve the problem that the wall thickness of the micro-channel cannot meet the heat transfer requirements, and the problem of thermal resistance has not been solved. It is difficult to choose aluminum tube profiles and other issues
- Summary
- Abstract
- Description
- Claims
- Application Information
AI Technical Summary
Problems solved by technology
Method used
Image
Examples
Embodiment 1
[0043] The structure of the microchannel heat exchanger of the present invention is as figure 1 , figure 2 As shown, it includes a heat exchange section 1, and the heat exchange section 1 is formed by stacking several unit layers, and each unit layer is a refrigerant layer 11, a separator layer 12, and a working fluid layer 13 in sequence, as shown in image 3 As shown; several microchannels are distributed on the refrigerant layer 11 and the working fluid layer 13 . The cross-section of each of the microchannels is square, and the sides of the micropore channels in the working fluid layer are flush with the side surfaces of the microchannels in the adjacent refrigerant layer. The ratio of the hydraulic diameter of the microchannels in the refrigerant layer 11 to the hydraulic diameter of the microchannels in the working fluid layer 13 is 1:2.
[0044] The microchannel heat exchanger also includes a working fluid inlet 2, a working fluid inlet supporting a rectifying porti...
Embodiment 2
[0059] The structure of the microchannel heat exchanger of this embodiment is roughly the same as that described in Example 1, the difference is that the cross section of each microchannel is circular, and the hydraulics of the microchannels of the refrigerant layer 11 The diameter is 0.0675mm. The hydraulic diameter of the microchannels in the working fluid layer 11 is 1.0125 mm. The refrigerant layer 11, the partition layer 12, and the working fluid layer 13 are made of copper. Heat exchangers using the above materials and sizes will slightly reduce the heat transfer performance, but can improve the flow characteristics of the working fluid, and it will be inconvenient in the selection of manufacturing materials. According to the physical properties of the refrigerant and working fluid used in the heat pump system, The overall performance is still within a reasonable range.
[0060] The method for manufacturing the microchannel heat exchange section 1 of the heat exchanger...
Embodiment 3
[0066] The structure of the microchannel heat exchanger of this embodiment is roughly the same as that described in Example 1, the difference is that the cross-section of each microchannel is elliptical, and the hydraulics of the microchannels of the refrigerant layer 11 The diameter is 0.5mm. The hydraulic diameter of the microchannels in the working fluid layer 11 is 0.125mm. The refrigerant layer 11, the separator layer 12, and the working fluid layer 13 are made of aluminum. Heat exchangers using the above materials and sizes will have improved heat transfer performance, increased flow pressure loss of the working fluid, and easy selection of manufacturing materials. According to the characteristics of the refrigerant and working fluid used in the heat pump system, The overall performance is still within a reasonable range.
[0067] The method for manufacturing the microchannel heat exchange section 1 of the heat exchanger comprises the following steps,
[0068] a. The ...
PUM
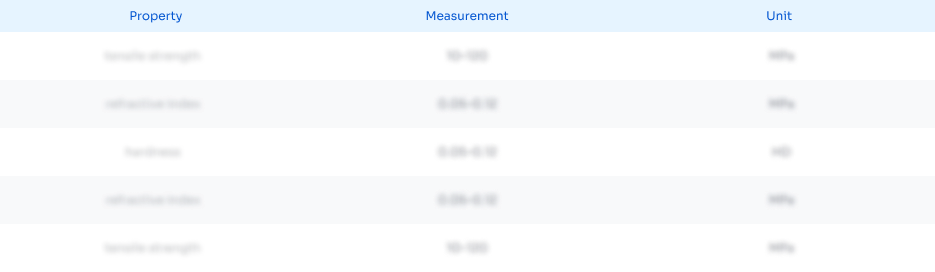
Abstract
Description
Claims
Application Information

- R&D
- Intellectual Property
- Life Sciences
- Materials
- Tech Scout
- Unparalleled Data Quality
- Higher Quality Content
- 60% Fewer Hallucinations
Browse by: Latest US Patents, China's latest patents, Technical Efficacy Thesaurus, Application Domain, Technology Topic, Popular Technical Reports.
© 2025 PatSnap. All rights reserved.Legal|Privacy policy|Modern Slavery Act Transparency Statement|Sitemap|About US| Contact US: help@patsnap.com