Method for recycling magnesium from middle-low grade high-magnesium phosphate rock
A high-magnesium phosphate rock, low-grade technology, applied in the field of magnesium recovery, can solve the problems of phosphorus loss, strong acidity of the compound demagnesizing agent, etc., and achieve the effects of small phosphorus loss, high efficiency, simple and reliable process
- Summary
- Abstract
- Description
- Claims
- Application Information
AI Technical Summary
Problems solved by technology
Method used
Examples
Embodiment 1
[0033] (1) Take medium and low-grade high-magnesium phosphate rock (P 2 o 5 content of 25.2%, MgO content of 3.14%, MgO / P 2 o 5 is 12.46%) and ground into phosphate rock powder, the fineness of which is 80% and passed through a 100-mesh sieve. Get 650 grams of ore powder in the reaction tank, add water 1625g and stir. The temperature of the water bath is raised to 60°C, and the magnesium removal agent (obtained by mixing 50 parts of 98% concentrated sulfuric acid and 50 parts of magnesium sulfate) is added to adjust the pH value to 3.5. Stop adding the magnesium removal agent. Keep the temperature at 60°C and stir for 2 hours to dissolve the magnesium in the phosphate rock under the action of acid.
[0034] (2) The demagnesization reaction slurry is separated from solid and liquid by means of forced vacuum filtration (centrifugal treatment can be used when the equivalent is large), and the filter cake is washed with an appropriate amount of water. The filter cake is magne...
Embodiment 2
[0041] (1) Take medium and low-grade high-magnesium phosphate rock (P 2 o 5 content of 25.2%, MgO content of 3.14%, MgO / P 2 o 5 is 12.46%) and ground into phosphate rock powder, the fineness of which is 80% and passed through a 100-mesh sieve. Take 600g of ore powder in the reaction tank, add 1800g of water to stir, take a water bath to 60°C, add magnesium hydrogen sulfate to adjust the pH value to 4.0, stop adding the magnesium hydrogen sulfate, add 220.6g of magnesium hydrogen sulfate, and keep the temperature of the water bath constant To 60 ℃, stirring reaction for 120min, so that the magnesium in the phosphate rock is dissolved under the action of acid.
[0042] (2) The solid-liquid separation of the magnesium removal reaction slurry is carried out by means of forced vacuum filtration, and the filter cake is washed with an appropriate amount of water. The filter cake is magnesium dephosphorylated concentrate, which can enter the production of wet-process phosphoric ac...
Embodiment 3
[0049] (1) Take medium and low-grade high-magnesium phosphate rock (P 2 o 5 content of 25.2%, MgO content of 3.14%, MgO / P 2 o 5 is 12.46%) and ground into phosphate rock powder, the fineness of which is 80% and passed through a 100-mesh sieve. .Put 650g of ore powder in the reaction tank, add 1300g of water and stir the water bath to 60°C, add magnesium removal agent (obtained by mixing 55 parts of 98% concentrated sulfuric acid and 45 parts of magnesium sulfate) and adjust the pH value to 3.0. Stop adding magnesium removal agent Add a total of 212.4g of demagnesizing agent, keep the temperature of the water bath to 50°C, stir and react for 120min, so that the magnesium in the phosphate rock is dissolved under the action of acid.
[0050] (2) The solid-liquid separation of the magnesium removal reaction slurry is carried out by means of forced vacuum filtration, and the filter cake is washed with an appropriate amount of water. The filter cake is magnesium dephosphorylated...
PUM
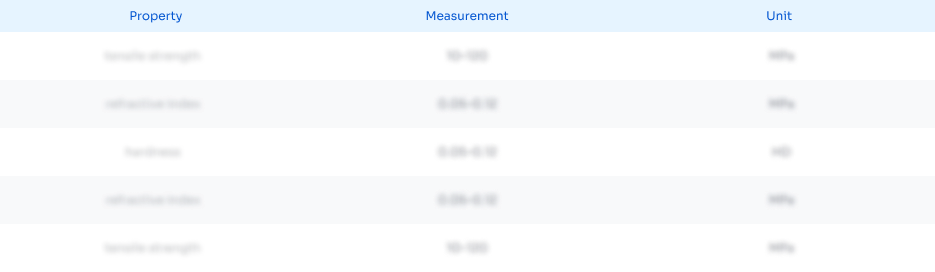
Abstract
Description
Claims
Application Information

- Generate Ideas
- Intellectual Property
- Life Sciences
- Materials
- Tech Scout
- Unparalleled Data Quality
- Higher Quality Content
- 60% Fewer Hallucinations
Browse by: Latest US Patents, China's latest patents, Technical Efficacy Thesaurus, Application Domain, Technology Topic, Popular Technical Reports.
© 2025 PatSnap. All rights reserved.Legal|Privacy policy|Modern Slavery Act Transparency Statement|Sitemap|About US| Contact US: help@patsnap.com