Displacement-force compound control lifting system for forging manipulator
A lifting system and composite control technology, applied in forging/pressing/hammering machinery, mechanical equipment, manufacturing tools, etc., can solve the problem of inability to meet the high-efficiency work of manipulators, the inability to realize the control of lifting force, and the low frequency response of proportional pressure valves and other problems, to achieve the effect of simple structure and control strategy, reduced resistance, and reliable work
- Summary
- Abstract
- Description
- Claims
- Application Information
AI Technical Summary
Problems solved by technology
Method used
Image
Examples
Embodiment 1
[0018] Embodiment 1. A displacement-force composite control lift system for a forging manipulator, which consists of an oil supply port 1, a proportional servo valve 2, a safety valve 3, a one-way valve 4, a stop valve 5, and a left lift cylinder 6-1 , right lifting cylinder 6-2, oil source and oil return port 7, displacement sensor 8, pressure sensor 12 and displacement-force composite controller 20.
[0019] Port P of proportional servo valve 2 is connected to oil supply port 1 of the oil source; port B of proportional servo valve 2 is sealed; port A of proportional servo valve 2 is connected to the inlet of safety valve 3, the outlet of one-way valve 4, the inlet of stop valve 5, the pressure Sensor 12, left lift cylinder 6-1 lower chamber connected with right lift cylinder 6-2 lower chamber; oil source return port 7 and T port of proportional servo valve 2, safety valve 3 outlet, one-way valve 4 inlet, stop valve 5 outlet, left lifting cylinder 6-1 upper cavity, right lift...
PUM
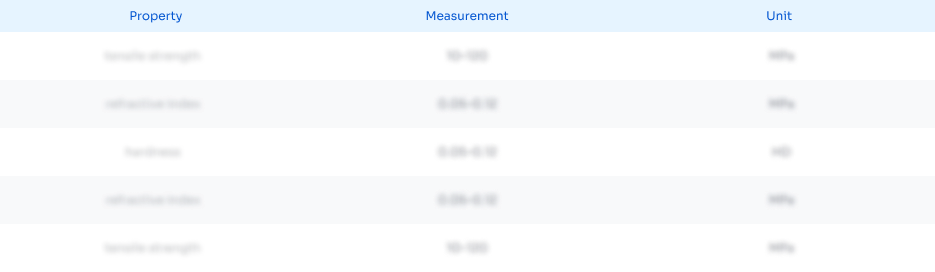
Abstract
Description
Claims
Application Information

- R&D
- Intellectual Property
- Life Sciences
- Materials
- Tech Scout
- Unparalleled Data Quality
- Higher Quality Content
- 60% Fewer Hallucinations
Browse by: Latest US Patents, China's latest patents, Technical Efficacy Thesaurus, Application Domain, Technology Topic, Popular Technical Reports.
© 2025 PatSnap. All rights reserved.Legal|Privacy policy|Modern Slavery Act Transparency Statement|Sitemap|About US| Contact US: help@patsnap.com