Flue gas waste heat recovery method for rotary kiln
A technology of flue gas waste heat and recovery method, applied in rotary drum furnace, waste heat treatment, climate sustainability, etc., can solve the problem of increasing smoke exhaust resistance of rotary kiln pre-firing system, the influence of permanent magnet ferrite powder quality, and kiln temperature To improve the return on investment, reduce the implementation investment, and improve the economic performance
- Summary
- Abstract
- Description
- Claims
- Application Information
AI Technical Summary
Problems solved by technology
Method used
Image
Examples
Embodiment Construction
[0010] specific implementation
[0011] The present invention will now be described with reference to the accompanying drawings and embodiments.
[0012] like figure 1 Shown is a method for recovering waste heat from flue gas from a rotary kiln. The method is to install a heat exchanger 3 that is resistant to high temperature, resists high temperature corrosion and effectively solves the problem of thermal expansion on the exhaust pipe 2 of the rotary kiln 1. The waste heat of the flue gas high temperature area of the rotary kiln 1 is recovered, and at the same time, a heat exchanger 4 that is always adaptive to maintain a high wall temperature and resists low temperature corrosion of the corrosive components in the flue gas is set to recover the waste heat of the flue gas low temperature area of the rotary kiln 1. The heat exchanger 4 is connected in series On the flue gas outlet side of the heat exchanger 3, the heat exchanger 3 and the heat user 6 are connected to eac...
PUM
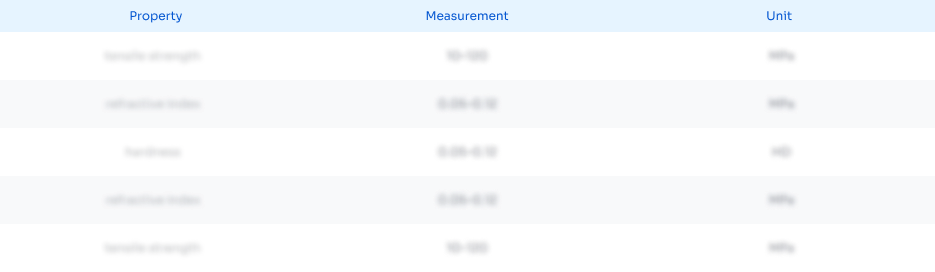
Abstract
Description
Claims
Application Information

- R&D
- Intellectual Property
- Life Sciences
- Materials
- Tech Scout
- Unparalleled Data Quality
- Higher Quality Content
- 60% Fewer Hallucinations
Browse by: Latest US Patents, China's latest patents, Technical Efficacy Thesaurus, Application Domain, Technology Topic, Popular Technical Reports.
© 2025 PatSnap. All rights reserved.Legal|Privacy policy|Modern Slavery Act Transparency Statement|Sitemap|About US| Contact US: help@patsnap.com