Refining furnace dehydrogenation method
A refining furnace and dehydrogenation technology, applied in the field of refining furnace dehydrogenation, can solve the problems of inability to use RH furnace for dehydrogenation, affecting the dehydrogenation effect, and slag on the surface of molten steel.
- Summary
- Abstract
- Description
- Claims
- Application Information
AI Technical Summary
Problems solved by technology
Method used
Examples
Embodiment 1
[0026] The type of steel smelted in this embodiment is P20HL, 90t ladle, and the smelting process route of this steel is converter→LF→single nozzle refining furnace→CCM. Adjust the temperature and composition of the molten steel to the target content before the molten steel enters the single nozzle refining furnace for treatment.
[0027] The initial conditions of the single nozzle refining furnace are: molten steel temperature 1611°C, vertical distance from the free space of the ladle (that is, the vertical distance from the slag surface to the upper edge of the ladle) 450mm, the thickness of the slag layer is 100mm, and the weight of molten steel is 80.75t.
[0028] The weight percentage ratio of the molten steel components before treatment in the single nozzle refining furnace is:
[0029] C 0.30%; Si 0.47%; Mn 0.87%; P 0.012%;
[0030] S 0.0056%; Al 0.03%; H 4.7ppm
[0031] The rest is Fe and unavoidable impurities.
[0032] The embodiment steps of the method for this r...
Embodiment 2
[0043] The type of steel smelted in this embodiment is P265GH, 90t ladle, and the smelting process route of this steel is converter→LF→single nozzle refining furnace→CCM. Adjust the temperature and composition of the molten steel to the target content before the molten steel enters the single nozzle refining furnace for treatment.
[0044] The initial conditions of the single-nozzle refining furnace are: molten steel temperature 1654°C, vertical distance from the free space of the ladle (that is, the vertical distance from the slag surface to the upper edge of the ladle) is 400mm, the thickness of the slag layer is 100mm, and the weight of molten steel is 84.7t.
[0045] The weight percentage ratio of the molten steel components before treatment in the single nozzle refining furnace is:
[0046] C 0.155%; Si 0.25%; Mn 1.29%; P 0.015%;
[0047] S 0.0063%; Al 0.03%; H 5.4ppm
[0048] The rest is Fe and unavoidable impurities.
[0049] The steps of the method embodiment of thi...
Embodiment 3
[0060] The type of steel smelted in this embodiment is 718HL, 90t ladle, and the smelting process route of this steel is converter→LF→single nozzle refining furnace→CCM. Adjust the temperature and composition of the molten steel to the target content before the molten steel enters the single nozzle refining furnace for treatment.
[0061] The initial conditions of the single-nozzle refining furnace are: molten steel temperature 1601°C, vertical distance from the free space of the ladle (that is, the vertical distance from the slag surface to the upper edge of the ladle) 450mm, the thickness of the slag layer is 90mm, and the weight of molten steel is 81.9t.
[0062] The weight percentage ratio of the molten steel components before treatment in the single nozzle refining furnace is:
[0063] C 0.33%; Si 0.24%; Mn 1.34%; P 0.009%;
[0064] S 0.005%; Al 0.078%; H 6.2ppm;
[0065] The rest is Fe and unavoidable impurities.
[0066] The steps of the method embodiment of this ref...
PUM
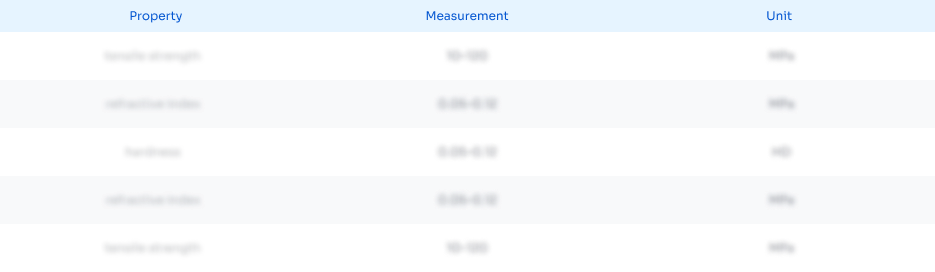
Abstract
Description
Claims
Application Information

- R&D
- Intellectual Property
- Life Sciences
- Materials
- Tech Scout
- Unparalleled Data Quality
- Higher Quality Content
- 60% Fewer Hallucinations
Browse by: Latest US Patents, China's latest patents, Technical Efficacy Thesaurus, Application Domain, Technology Topic, Popular Technical Reports.
© 2025 PatSnap. All rights reserved.Legal|Privacy policy|Modern Slavery Act Transparency Statement|Sitemap|About US| Contact US: help@patsnap.com