Process for manufacturing integral chassis towing beam for railway passenger vehicle
The invention relates to a railway passenger car and manufacturing process technology, which is applied in the field of the manufacturing process of the integral underframe traction beam of the railway passenger car, and can solve the problems of low assembly precision of the sleeper beam and high stress of the corrugated floor behind the sleeper, and achieve good market prospects, reliable quality and production efficiency. high effect
- Summary
- Abstract
- Description
- Claims
- Application Information
AI Technical Summary
Problems solved by technology
Method used
Image
Examples
Embodiment Construction
[0029] Such as Figure 1-3 As shown, it is the expanded view and structural schematic diagram of the draw beam of this embodiment.
[0030] The manufacturing process of the traction beam of the integrated underframe of the railway passenger car in this embodiment specifically includes the following steps:
[0031] The first step is steel plate shot peening pretreatment, spraying zinc silicate pre-coating primer on the steel plate;
[0032] The second step, cutting and blanking - cutting and blanking by laser cutting machine (or water jetting machine), the blanking parts after cutting include the main board 1, the corbel side 11 of the main board 1 is equal to the corbel height, and the end of the main board 1 The beam side 12 is equal to the height of the end beam, the upper end of the main board 1 along the corbel side 11 to the end beam side 12 is the first upper airfoil 21 and the second upper airfoil 22 in turn, and the lower end of the main board 1 is along the corbel si...
PUM
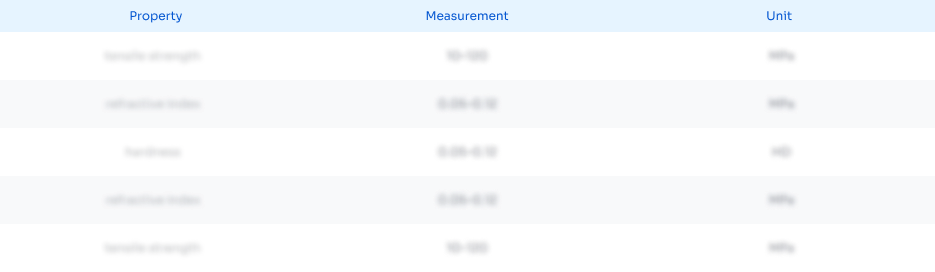
Abstract
Description
Claims
Application Information

- Generate Ideas
- Intellectual Property
- Life Sciences
- Materials
- Tech Scout
- Unparalleled Data Quality
- Higher Quality Content
- 60% Fewer Hallucinations
Browse by: Latest US Patents, China's latest patents, Technical Efficacy Thesaurus, Application Domain, Technology Topic, Popular Technical Reports.
© 2025 PatSnap. All rights reserved.Legal|Privacy policy|Modern Slavery Act Transparency Statement|Sitemap|About US| Contact US: help@patsnap.com