Production method capable of reducing internal air holes of monocrystalline silicon
A technology of internal pores and production methods, applied in the directions of single crystal growth, single crystal growth, crystal growth, etc., can solve the problems of time, human and financial waste, and cost reduction
- Summary
- Abstract
- Description
- Claims
- Application Information
AI Technical Summary
Problems solved by technology
Method used
Examples
Embodiment 1
[0018] A production method for reducing the internal pores of monocrystalline silicon. When starting to work, first clean the thermal system in the furnace, then place the polycrystalline silicon solid in a quartz crucible, close the furnace door and turn on the vacuum pump to evacuate the furnace. Then open the argon valve to fill the furnace with argon, the argon flow can be controlled by adjusting the argon valve, and the pressure in the furnace can be controlled by adjusting the argon valve and vacuum pump; after that, the heating system is turned on to heat the material, at this time Set the filled argon gas flow rate to 10L / min, and the pressure in the furnace to 280Pa, so that most of the bubbles in the silicon liquid or the crucible can be eliminated by using a high vacuum degree;
[0019] After the chemical material is completed, it enters the heat preservation and stabilization stage. At this time, the crucible starts to rotate, and the rotation speed of the crucible ...
Embodiment 2
[0023] The difference between this embodiment and embodiment 1 is:
[0024] ① In the step of heating silicon materials, the flow rate of argon gas is 12 L / min, and the pressure in the furnace is 350 Pa;
[0025] ② In the single crystal necking step, the flow rate of argon gas is 22 L / min, and the pressure in the furnace is 650Pa.
[0026] The test results show that through the improvement of the above steps, the pore content in the solid single crystal is reduced by 27.3% on average.
Embodiment 3
[0028] The difference between this embodiment and embodiment 1 is:
[0029] ①In the step of heating silicon material, the flow rate of argon gas is 13 L / min, and the pressure in the furnace is 400 Pa;
[0030] ②In the single crystal necking step, the flow rate of argon gas is 25 L / min, and the pressure in the furnace is 700Pa.
[0031] The test results show that through the improvement of the above steps, the pore content in the solid single crystal is reduced by 29.7% on average.
PUM
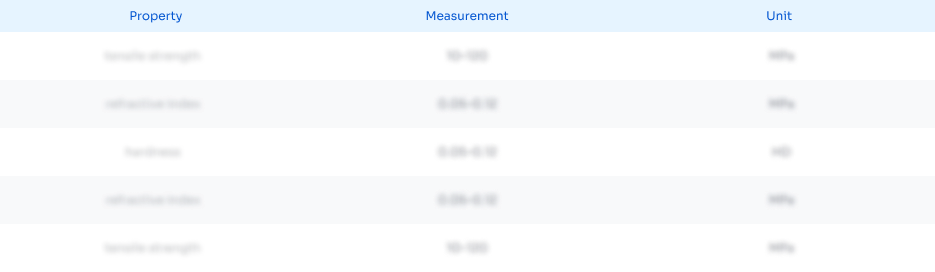
Abstract
Description
Claims
Application Information

- R&D Engineer
- R&D Manager
- IP Professional
- Industry Leading Data Capabilities
- Powerful AI technology
- Patent DNA Extraction
Browse by: Latest US Patents, China's latest patents, Technical Efficacy Thesaurus, Application Domain, Technology Topic, Popular Technical Reports.
© 2024 PatSnap. All rights reserved.Legal|Privacy policy|Modern Slavery Act Transparency Statement|Sitemap|About US| Contact US: help@patsnap.com