Hot bulge forming apparatus, a hot bulge forming method and a product formed through hot bulge forming
A technology of formed products and thermal expansion, applied in the direction of forming tools, metal processing equipment, manufacturing tools, etc., can solve the problems of shrinkage of workpieces, reduction of pushing force, etc.
- Summary
- Abstract
- Description
- Claims
- Application Information
AI Technical Summary
Problems solved by technology
Method used
Image
Examples
Embodiment Construction
[0039] Hereinafter, one embodiment of the present invention will be described with reference to the drawings.
[0040] figure 1 It is a flowchart showing the operation of the thermal expansion molding device 1 according to one embodiment of the present invention.
[0041] figure 2 It is a perspective view showing tubular blanks 10 a to 10 d which are workpieces formed by the thermal expansion molding apparatus 1 .
[0042] The thermal expansion forming device 1 performs the following steps in the following order: energized heating step 2, tube expansion forming step 3 as a preliminary forming step, crush forming step 4, and cross-section forming step 5 as a final forming step.
[0043] Specifically, in the energization heating step 2, the tubular blank 10a made of an aluminum alloy extending substantially linearly is heated.
[0044] In the pipe expansion forming step 3, the first expansion forming device 6 (refer to image 3 ), expand the portions near both ends of the ...
PUM
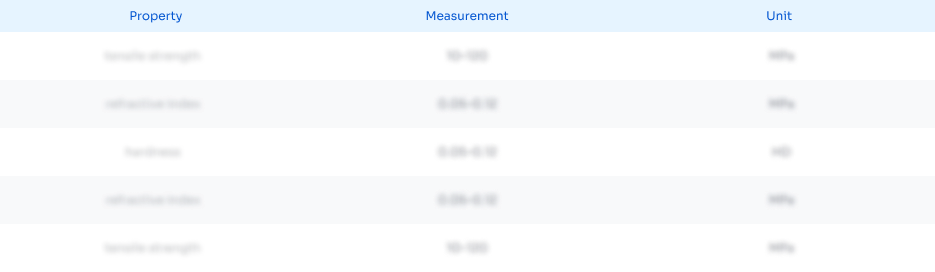
Abstract
Description
Claims
Application Information

- R&D Engineer
- R&D Manager
- IP Professional
- Industry Leading Data Capabilities
- Powerful AI technology
- Patent DNA Extraction
Browse by: Latest US Patents, China's latest patents, Technical Efficacy Thesaurus, Application Domain, Technology Topic, Popular Technical Reports.
© 2024 PatSnap. All rights reserved.Legal|Privacy policy|Modern Slavery Act Transparency Statement|Sitemap|About US| Contact US: help@patsnap.com