Method for automatically correcting differential-pressure compensation factors of weighing of top charging bucket
A self-correction and weighing technology, which is applied in the field of differential pressure compensation self-correction of furnace top tank weighing, can solve problems such as linear compensation coefficient drift, avoid large fluctuations, reduce manual adjustments, and improve automation levels Effect
- Summary
- Abstract
- Description
- Claims
- Application Information
AI Technical Summary
Problems solved by technology
Method used
Image
Examples
Embodiment Construction
[0032] First the principles involved in the present invention are analyzed:
[0033] figure 1 It is a system structure diagram provided by the present invention, wherein the whole system is composed of PLC controller, furnace top weighing and measuring device, pressure transmitter and upper computer. The PLC controller receives the data sent back from the on-site furnace top weighing measuring device and pressure transmitter, analyzes and calculates the data according to the current operating status of the blast furnace, periodically corrects the compensation data, and saves the corrected data in the PLC In the memory database of the controller, and displayed on the host computer.
[0034] Under the normal production conditions of the blast furnace, the pressure on the top of the furnace is always at a high pressure of 1.5 to 2.5 kg. Under the action of the pressure on the top of the furnace, the material tank is subjected to a buoyancy force proportional to the cross-section...
PUM
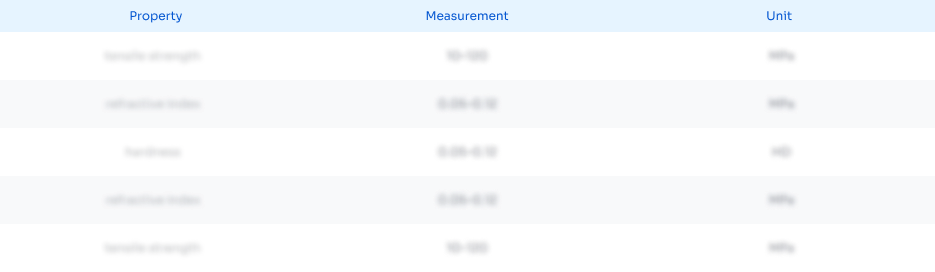
Abstract
Description
Claims
Application Information

- Generate Ideas
- Intellectual Property
- Life Sciences
- Materials
- Tech Scout
- Unparalleled Data Quality
- Higher Quality Content
- 60% Fewer Hallucinations
Browse by: Latest US Patents, China's latest patents, Technical Efficacy Thesaurus, Application Domain, Technology Topic, Popular Technical Reports.
© 2025 PatSnap. All rights reserved.Legal|Privacy policy|Modern Slavery Act Transparency Statement|Sitemap|About US| Contact US: help@patsnap.com