Alkaline non-cyanide copper plating solution taking amino methylene diphosphonic acid as main coordinating agent
A technology of aminomethylene diphosphonic acid and cyanide-free copper plating, which is applied in the field of surface treatment and can solve the problems of low cathodic current efficiency, low deep plating capacity, and environmental pollution in cyanide plating solutions
- Summary
- Abstract
- Description
- Claims
- Application Information
AI Technical Summary
Problems solved by technology
Method used
Image
Examples
Embodiment 1
[0015] An alkaline cyanide-free copper plating solution composed of aminomethylene diphosphonic acid as the main complexing agent was prepared according to the following proportions.
[0016] Aminomethylene diphosphonic acid (AMDP) 70g / L
[0017] Copper sulfate pentahydrate 20g / L
[0018] Potassium hydroxide 80g / L
[0019] Potassium carbonate 40g / L
[0020] pH 9.7
[0021] Dissolve and mix the weighed aminomethylene diphosphonic acid and copper sulfate pentahydrate with deionized water, add potassium hydroxide solution while stirring, and finally add a certain amount of potassium carbonate and stir until completely dissolved.
[0022] In the obtained solution, adjust the temperature of the solution to 25°C, and the cathode current density is 1.5A / dm 2 Copper plating of about 6 microns is plated on the Φ2mm steel wire substrate, and the electroplating time is 15 minutes. According to ASTMB452-2002, the binding force is tested by winding method.
Embodiment 2
[0024] An alkaline cyanide-free copper plating solution composed of aminomethylene diphosphonic acid as the main complexing agent was prepared according to the following proportions.
[0025] Aminomethylene diphosphonic acid (AMDP) 82g / L
[0026] Copper chloride dihydrate 28g / L
[0027] Sodium hydroxide 75g / L
[0028] Sodium carbonate 50g / L
[0029] pH 9.2
[0030] Dissolve and mix the weighed aminomethylene diphosphonic acid and copper chloride dihydrate with deionized water respectively, add sodium hydroxide solution while stirring, and finally add quantitative sodium carbonate and stir until completely dissolved.
[0031]Zinc die-casting parts that have been pre-treated by ultrasonic degreasing and activation are charged into the tank for electroplating in the above solution. During electroplating, the temperature of the solution is controlled at 50°C and the cathode current density is 3A / dm. 2 , Plating time is 10 minutes. According to the electronic industry standard...
PUM
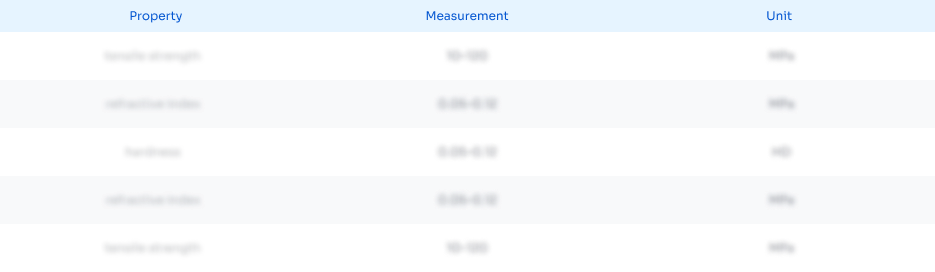
Abstract
Description
Claims
Application Information

- R&D
- Intellectual Property
- Life Sciences
- Materials
- Tech Scout
- Unparalleled Data Quality
- Higher Quality Content
- 60% Fewer Hallucinations
Browse by: Latest US Patents, China's latest patents, Technical Efficacy Thesaurus, Application Domain, Technology Topic, Popular Technical Reports.
© 2025 PatSnap. All rights reserved.Legal|Privacy policy|Modern Slavery Act Transparency Statement|Sitemap|About US| Contact US: help@patsnap.com