Method for adsorbing phosphorus pollutants in water by using waste residues in iron and steel industry
A phosphorus pollutant and iron and steel industry technology, applied in the direction of adsorption water/sewage treatment, chemical instruments and methods, and other chemical processes, can solve the problems of occupying abandoned land or fertile land, affecting the ecological environment, etc., and achieve good adsorption, The effect of lower concentration and higher phosphorus removal rate
- Summary
- Abstract
- Description
- Claims
- Application Information
AI Technical Summary
Problems solved by technology
Method used
Image
Examples
Embodiment 1
[0025] A method for utilizing iron and steel industry waste slag to adsorb phosphorus pollutants in water, comprising the steps of:
[0026] 1) Crush the steel slag to 5-10 mesh, wash it with distilled water, dry it, and set aside; grind the iron tailings to 200 mesh, set aside;
[0027] Then according to the mass percentage of each raw material: steel slag 50%, iron tailings 40%, binding agent 10%, select steel slag, iron tailings and binding agent, mix, obtain composite material, standby; The agent is water glass, and the modulus of water glass is 1.5 to 3.5;
[0028] 2) Spread the composite material in a container (such as a large ash dish) and put it into a high-temperature resistance furnace for roasting, raise the temperature to 100°C at 6°C / min (slowly), keep it warm for 60min, and let the physical moisture in the composite material (raw meal) evaporate ; Then raise the temperature to 750°C at 11°C / min, keep it warm for 1.2h, and cool down to room temperature naturally...
Embodiment 2
[0059] A method for utilizing iron and steel industry waste slag to adsorb phosphorus pollutants in water, comprising the steps of:
[0060] 1) Crush the steel slag to 5-10 mesh, wash it with distilled water, dry it, and set aside; grind the iron tailings to 200 mesh, set aside;
[0061] Then according to the mass percentage of each raw material: steel slag 45%, iron tailings 45%, binding agent 10%, select steel slag, iron tailings and binding agent, mix, obtain composite material, standby; The agent is cement;
[0062] 2) Spread the composite material in a container (such as a large ash dish) and put it into a high-temperature resistance furnace for roasting, raise the temperature to 100°C at 4°C / min (slowly), keep it warm for 60 minutes, and let the physical moisture in the composite material (raw meal) evaporate ;Then raise the temperature to 700°C at 12°C / min, keep it warm for 1h, and cool down to room temperature naturally to obtain the adsorption material;
[0063] 3) ...
Embodiment 3
[0065] A method for utilizing iron and steel industry waste slag to adsorb phosphorus pollutants in water, comprising the steps of:
[0066] 1) Crush the steel slag to 5-10 mesh, wash it with distilled water, dry it, and set aside; grind the iron tailings to 200 mesh, set aside;
[0067] Then according to the mass percentage of each raw material: steel slag 55%, iron tailings 35%, binding agent 10%, select steel slag, iron tailings and binding agent, mix, obtain composite material, standby; The agent is water glass, and the modulus of water glass is 1.5 to 3.5;
[0068] 2) Spread the composite material in a container (such as a large ash dish) and put it into a high-temperature resistance furnace for roasting, raise the temperature at 8°C / min (slowly) to 100°C, and keep it warm for 60 minutes to allow the physical moisture in the composite material (raw meal) to evaporate ; Then raise the temperature to 750°C at 10°C / min, keep it warm for 1.5h, and cool down to room temperatu...
PUM
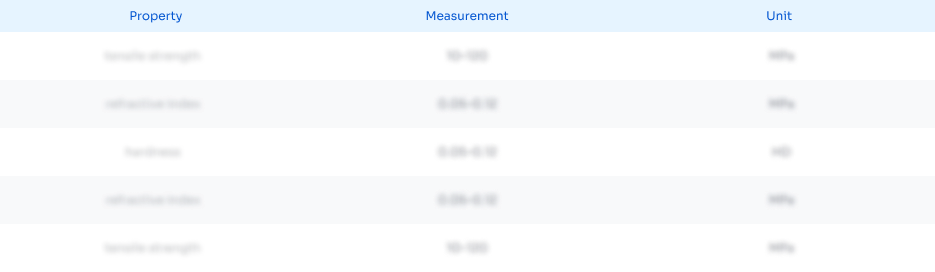
Abstract
Description
Claims
Application Information

- R&D Engineer
- R&D Manager
- IP Professional
- Industry Leading Data Capabilities
- Powerful AI technology
- Patent DNA Extraction
Browse by: Latest US Patents, China's latest patents, Technical Efficacy Thesaurus, Application Domain, Technology Topic, Popular Technical Reports.
© 2024 PatSnap. All rights reserved.Legal|Privacy policy|Modern Slavery Act Transparency Statement|Sitemap|About US| Contact US: help@patsnap.com