Computational fluid dynamics (CFD)-based centrifugal pump multi-working condition hydraulic power optimization method
A hydraulic optimization and centrifugal pump technology, which is applied in the direction of pumps, non-variable pumps, non-displacement pumps, etc., can solve problems such as hydraulic optimization methods for multi-working conditions of centrifugal pumps that have not been seen in CFD, and achieve the goal of suppressing cavitation Effect
- Summary
- Abstract
- Description
- Claims
- Application Information
AI Technical Summary
Problems solved by technology
Method used
Image
Examples
Embodiment Construction
[0031] The present invention will be further described in detail with reference to the accompanying drawings and embodiments.
[0032] The flow of the CFD-based hydraulic optimization method for multi-working conditions of centrifugal pumps in this embodiment is as follows figure 1 shown, including the following steps:
[0033] (1) Based on the external characteristic experiment, the initial sample library for the multi-condition hydraulic optimization of the centrifugal pump is established.
[0034] Build a test bench for the external characteristics of centrifugal pumps; lift of centrifugal pumps H It is measured by the pressure gauges at the inlet and outlet of the centrifugal pump; the power of the centrifugal pump is measured by the electric method P ; Centrifugal pump flow Q It is read by the electromagnetic flowmeter on the outlet piping system of the centrifugal pump; the efficiency of the centrifugal pump n by the formula n = ρ g QH / P .
[0035] The key ...
PUM
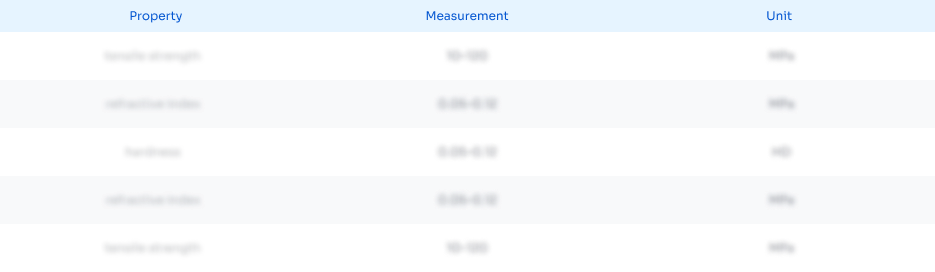
Abstract
Description
Claims
Application Information

- R&D
- Intellectual Property
- Life Sciences
- Materials
- Tech Scout
- Unparalleled Data Quality
- Higher Quality Content
- 60% Fewer Hallucinations
Browse by: Latest US Patents, China's latest patents, Technical Efficacy Thesaurus, Application Domain, Technology Topic, Popular Technical Reports.
© 2025 PatSnap. All rights reserved.Legal|Privacy policy|Modern Slavery Act Transparency Statement|Sitemap|About US| Contact US: help@patsnap.com