Formula of tungstate and cobalt hard alloy
A cemented carbide and formula technology, applied in the field of tungsten-cobalt cemented carbide formula, can solve the problems of uniform grain distribution, unenhanced thermal fatigue resistance and wear resistance, difficulty, etc., and achieve obvious wear resistance and heat resistance. The effect of fatigue performance
- Summary
- Abstract
- Description
- Claims
- Application Information
AI Technical Summary
Problems solved by technology
Method used
Image
Examples
Embodiment 1
[0012] A tungsten-cobalt cemented carbide formula, comprising the following components, the WC powder mass percentage is 92%, the cobalt powder mass percentage is 8%, wherein the coarse particle WC powder accounts for 65% of the WC powder weight, and the fine particle WC accounts for the WC powder. 35% of powder weight, the coarse particle WC powder is 2.2 μm, and the fine particle WC powder is 0.7 μm.
Embodiment 2
[0014] A tungsten-cobalt cemented carbide formula, comprising the following components, the WC powder mass percentage is 90%, the cobalt powder mass percentage is 10%, wherein the coarse particle WC powder accounts for 60% of the WC powder weight, and the fine particle WC accounts for WC powder 40% of the powder weight, the coarse particle WC powder is 2.4 μm, and the fine particle WC powder is 0.6 μm.
Embodiment 3
[0016] A tungsten-cobalt cemented carbide formula, comprising the following components, the WC powder mass percentage is 94%, the cobalt powder mass percentage is 6%, wherein the coarse particle WC powder accounts for 70% of the WC powder weight, and the fine particle WC accounts for WC 30% of the powder weight, the coarse particle WC powder is 2.0 μm, and the fine particle WC powder is 0.8 μm.
[0017] In the above three embodiments, after the various materials are prepared in proportion, they are made into hard powder by wet grinding, unloading, sedimentation, drying and vibrating screen, granulation with forming agent, compression molding, removal of forming agent, and sintering. quality alloy.
[0018] The two indicators of thermal fatigue and wear resistance require a two-way combination of powder grain size ratio and composition ratio to achieve an ideal requirement. Through this cemented carbide product with several ratios, thermal fatigue and wear resistance can be ach...
PUM
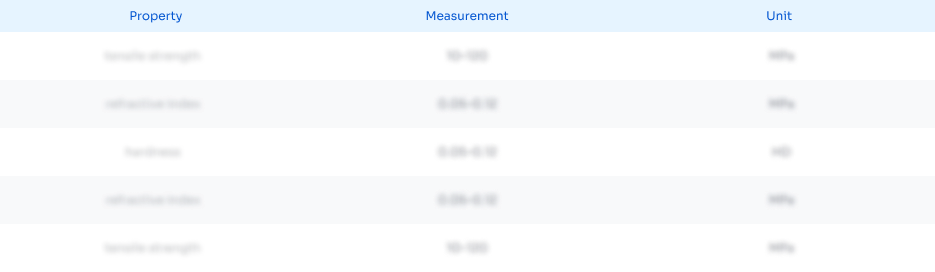
Abstract
Description
Claims
Application Information

- R&D
- Intellectual Property
- Life Sciences
- Materials
- Tech Scout
- Unparalleled Data Quality
- Higher Quality Content
- 60% Fewer Hallucinations
Browse by: Latest US Patents, China's latest patents, Technical Efficacy Thesaurus, Application Domain, Technology Topic, Popular Technical Reports.
© 2025 PatSnap. All rights reserved.Legal|Privacy policy|Modern Slavery Act Transparency Statement|Sitemap|About US| Contact US: help@patsnap.com