Composition of four-component lithium complex grease and preparation method thereof
A technology based on lubricating grease and lithium complex, which is applied in the field of lubricating grease, can solve the problems of poor bearing life, poor adhesion, and high bearing life, and achieve excellent high-temperature leakage prevention performance, excellent high-temperature leakage prevention performance, and high-temperature bearing life. Effect
- Summary
- Abstract
- Description
- Claims
- Application Information
AI Technical Summary
Problems solved by technology
Method used
Examples
Embodiment 1
[0023] Example 1 Add 500 grams of 12-hydroxystearic acid and 1900 grams of base oil 500SN into the reactor, heat to 80°C, put 31 grams of boric acid and 90 grams of lithium hydroxide into the alkali tank, dissolve it with 600 grams of water and heat to 80°C, put it into the reaction kettle, under the condition of 97°C, the reaction kettle is saponified and compounded in one step for 1.5 hours, and the saponified material is rapidly heated to 120°C, and the temperature is kept constant for half an hour. 69 grams of salicylic acid, stirred for 10 minutes, 121.5 grams of two-step alkali lithium hydroxide was dropped into an alkali tank and dissolved in 4 times of water to make an alkali solution, and the aqueous solution of the two-step alkali was added at 120° C. to carry out two-step saponification and compounding, adding After the lye is finished, the reaction kettle is heated slowly, and the temperature is kept at 134°C for one hour to ensure that the materials are fully mixed...
Embodiment 2
[0038] Example 2 Add 500 grams of 12-hydroxystearic acid and 1900 grams of base oil 500SN to the reactor, heat to 70°C, put 31 grams of boric acid and 90 grams of lithium hydroxide into the alkali tank, dissolve it with 600 grams of water and heat to 80°C, put it into the reaction kettle, under the condition of 97°C, the reaction kettle is saponified and compounded in one step for 1.5 hours, and the saponified material is rapidly heated to 120°C, and the temperature is kept constant for half an hour. 69 grams of salicylic acid, stirred for 20 minutes, 58 grams of the two-step alkali lithium hydroxide was dropped into the alkali tank and dissolved in 4 times of water to make an alkali solution, and the aqueous solution of the two-step alkali was added at 120 ° C to carry out two-step saponification and compounding. After the lye is finished, the temperature of the reaction kettle is raised slowly, and the temperature is kept at 134°C for one hour to ensure that the materials are...
Embodiment 3
[0053]Example 3 Add 500 grams of 12-hydroxystearic acid and 1900 grams of base oil 500SN into the reactor, heat to 90°C, put 31 grams of boric acid and 90 grams of lithium hydroxide into the alkali tank, dissolve and heat with 600 grams of water to 80°C, put it into the reaction kettle, and saponify and compound at 98°C for 1.5 hours. The saponified material is rapidly heated to 120°C, and the temperature is kept constant for half an hour. After the constant temperature is completed, 157 grams of azelaic acid and salicylic acid 69 grams of acid, stirred for 10 minutes, 96.5 grams of two-step alkali lithium hydroxide was put into the alkali tank and dissolved with 4 times of water to make an alkali solution. After the liquid, the reaction kettle is heated slowly, and kept at 131°C for one hour to ensure that the materials are fully mixed and dispersed to achieve the purpose of composite co-crystallization. It takes 3 hours to raise the temperature of the reaction kettle to 185°C...
PUM
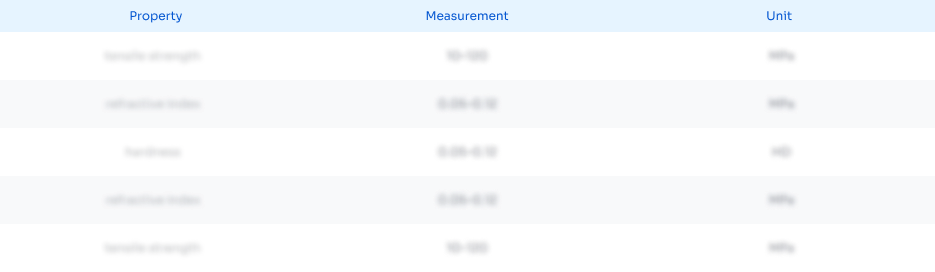
Abstract
Description
Claims
Application Information

- R&D
- Intellectual Property
- Life Sciences
- Materials
- Tech Scout
- Unparalleled Data Quality
- Higher Quality Content
- 60% Fewer Hallucinations
Browse by: Latest US Patents, China's latest patents, Technical Efficacy Thesaurus, Application Domain, Technology Topic, Popular Technical Reports.
© 2025 PatSnap. All rights reserved.Legal|Privacy policy|Modern Slavery Act Transparency Statement|Sitemap|About US| Contact US: help@patsnap.com