Corner glass piece toughening treatment process
A treatment process and technology for glass parts, which is applied in the field of tempering treatment of corner glass parts, and can solve problems such as easy damage, high self-explosion rate, and low yield
- Summary
- Abstract
- Description
- Claims
- Application Information
AI Technical Summary
Problems solved by technology
Method used
Image
Examples
Embodiment Construction
[0018] Below in conjunction with accompanying drawing and specific embodiment the present invention is described in further detail:
[0019] figure 1 As shown, the corner type glass part tempering treatment process of the present invention adopts the following steps: A) the glass plate 3 is sent into the heating furnace 1, and the glass plate is heated by a plurality of rod-shaped heaters 11 in the heating furnace 1. 3 for heating, the heater 11 is arranged on the upper and lower sides of the glass plate 3, the glass plate 3 moves back and forth on the roller 12 to reach the set temperature, and the glass plate 3 is taken out of the furnace to the hot bending mold chamber 2; B) the glass plate 3 Arriving in the mold chamber 2, one or more far-infrared heating tubes 21 are set above the predetermined bending point of the glass plate 3 to locally heat the glass plate 3, so that the local temperature at the bend of the glass plate 3 rises rapidly to soften the glass; C) when Whe...
PUM
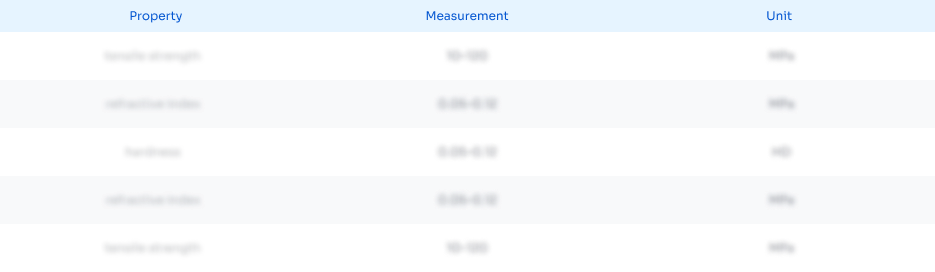
Abstract
Description
Claims
Application Information

- R&D
- Intellectual Property
- Life Sciences
- Materials
- Tech Scout
- Unparalleled Data Quality
- Higher Quality Content
- 60% Fewer Hallucinations
Browse by: Latest US Patents, China's latest patents, Technical Efficacy Thesaurus, Application Domain, Technology Topic, Popular Technical Reports.
© 2025 PatSnap. All rights reserved.Legal|Privacy policy|Modern Slavery Act Transparency Statement|Sitemap|About US| Contact US: help@patsnap.com