Casting method of crank case
A crankcase and spindle box technology, which is applied to casting molding equipment, molds, mold components, etc., can solve the problems of shrinkage porosity and uneven cooling speed, and achieve the possibility of eliminating shrinkage porosity, consistent cooling speed, and improved castings. quality effect
- Summary
- Abstract
- Description
- Claims
- Application Information
AI Technical Summary
Problems solved by technology
Method used
Examples
Embodiment 1
[0013] A crankcase casting method, the chemical composition of the crankcase is: C: 2.6%; Si: 1.6; Mn: 0.4%; S: 0.06%; Cr: 0.5%; Cu: 0.8%; Sn: 0.03 %; the rest is Fe;
[0014] Including the following steps:
[0015] A. Heat and smelt the above raw materials into molten metal at a melting temperature of 1480°C to 1500°C. After removing the slag, pour it into the ladle, and then put it into the holding furnace for heat preservation;
[0016] B. When the molten metal reaches 1420°C to 1450°C, put the molten metal into the ladle, add an inoculant 75Si to inoculate the molten metal, remove the slag quickly after the inoculation, and pour overnight;
[0017] C. Pouring pouring fluid into the sand mold through the gate, the pouring temperature is 1320°C-1330°C, and the spindle box is obtained after solidification; place a cold iron at the intersection of the thickness and thickness of the crankcase mold in the sand mold.
Embodiment 2
[0019] A crankcase casting method, the chemical composition of the crankcase is: C: 3.2%; Si: 2.2%; Mn: 1%; S: 0.08%; Cr: 1%; Cu: 1.0%; Sn: 0.03%; the rest is Fe;
[0020] Including the following steps:
[0021] A. Heat and smelt the above raw materials into molten metal at a melting temperature of 1480°C to 1500°C. After removing the slag, pour it into the ladle, and then put it into the holding furnace for heat preservation;
[0022] B. When the molten metal reaches 1420°C to 1450°C, put the molten metal into the ladle, add an inoculant 75Si to inoculate the molten metal, remove the slag quickly after the inoculation, and pour overnight;
[0023] C. Pouring pouring fluid into the sand mold through the gate, the pouring temperature is 1320°C to 1330°C, and the spindle box is obtained after solidification; place a cold iron at the intersection of the thickness and thickness of the crankcase mold in the sand mold.
PUM
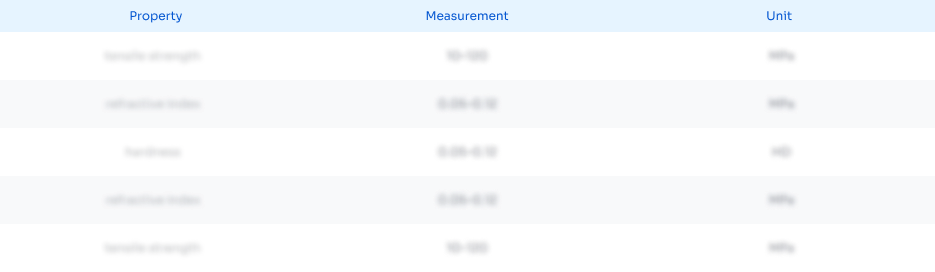
Abstract
Description
Claims
Application Information

- R&D
- Intellectual Property
- Life Sciences
- Materials
- Tech Scout
- Unparalleled Data Quality
- Higher Quality Content
- 60% Fewer Hallucinations
Browse by: Latest US Patents, China's latest patents, Technical Efficacy Thesaurus, Application Domain, Technology Topic, Popular Technical Reports.
© 2025 PatSnap. All rights reserved.Legal|Privacy policy|Modern Slavery Act Transparency Statement|Sitemap|About US| Contact US: help@patsnap.com