Manufacturing method for ultrathin tegular locking plate of nuclear reactor pressure vessel main bolt
A technology for pressure vessels and nuclear reactors, applied in the directions of bolts, screws, nuts, etc., can solve the problems of increased cost, low material utilization rate, complex structure, etc., and achieve the effects of low cost, accurate size and high material utilization rate
- Summary
- Abstract
- Description
- Claims
- Application Information
AI Technical Summary
Problems solved by technology
Method used
Image
Examples
Embodiment Construction
[0013] In the following, the method for manufacturing the ultra-thin tile-shaped locking piece of the main bolt of the nuclear reactor pressure vessel of the present invention will be further described in conjunction with the examples of the above-mentioned drawings.
[0014] The example involved in the method of the present invention includes a tubular forging 1, a chuck 2 at one end of the tubular forging 1, an annular pressure plate 3, a bolt 4, a screw 5, a pressure plate 6, a one-piece ultra-thin tile-shaped locking piece 7, a one-piece ultra-thin The waist-shaped hole 9 on the thin tile-shaped locking piece 7, the cutting line 10 and the single-piece ultra-thin tile-shaped locking piece 8 after cutting.
[0015] The method of the present invention is that one end of the tubular forging 1 with a wall thickness of 20mm, a diameter of 220mm and a length of 80mm is 20mm long and placed in the clamping position of the CNC lathe as a chuck, and the tubular forging 1 is moved to...
PUM
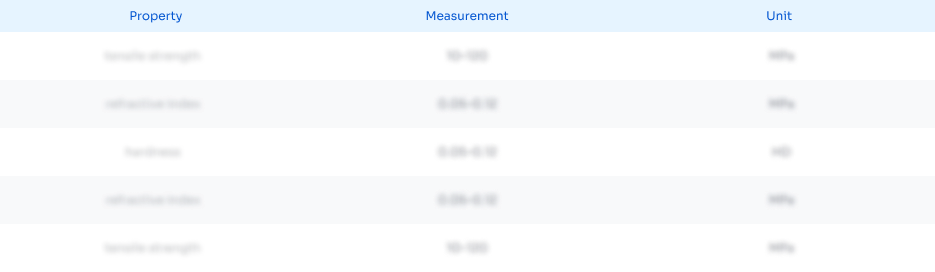
Abstract
Description
Claims
Application Information

- R&D Engineer
- R&D Manager
- IP Professional
- Industry Leading Data Capabilities
- Powerful AI technology
- Patent DNA Extraction
Browse by: Latest US Patents, China's latest patents, Technical Efficacy Thesaurus, Application Domain, Technology Topic, Popular Technical Reports.
© 2024 PatSnap. All rights reserved.Legal|Privacy policy|Modern Slavery Act Transparency Statement|Sitemap|About US| Contact US: help@patsnap.com